How a St. Thomas Resort Optimizes Wastewater Reuse
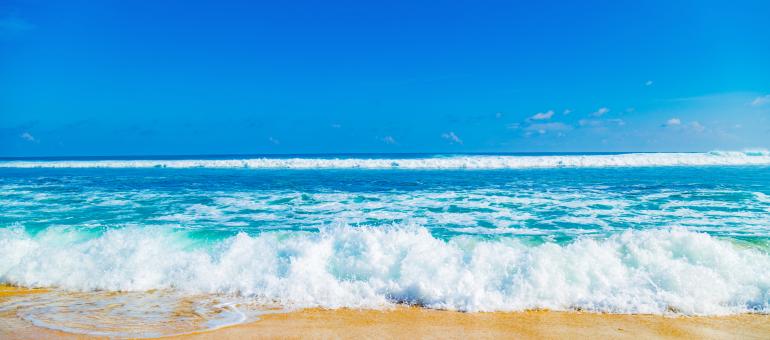
The U.S. Virgin Islands welcome more than 2 million tourists each year, a vital part of the economy considering tourism accounts for more than half of GDP and employment. With growing demands on limited water supplies across the islands, communities and businesses need innovative ways to stretch every drop.
St. Thomas, an island that’s home to 52,000 people, is particularly popular among tourists. A resort on the east end generates 40,000-80,000 gallons of wastewater per day and needs to treat the water so it can be reused. Before the resort engaged Veolia Water Technologies & Solutions in 2004, this water underwent conventional tertiary treatment before being discharged into the environment.
Nearly 20 years ago, Veolia implemented a membrane bioreactor (MBR) system to allow the resort to consistently achieve high-quality effluent beyond EPA requirements — less than 5 mg/L of total suspended solids (TSS) or biological oxygen demand (BOD).
The highly customized system incorporated existing concrete basins to reduce project costs. With this reliable, clean water source, the resort started reusing its MBR wastewater effluent for irrigation and flushing toilets. This reduced the need for desalination, eliminated effluent discharge into the environment, and allowed the resort to save on electricity and equipment costs.
Overcoming early challenges
MBR systems are dynamic in that they can help solve an array of problems. This was proved true for a few roadblocks the resort had to conquer.
Even though the basin geometry wasn’t ideal as a bioreactor, the resort’s MBR system lasted for more than a decade until 2016, when Veolia replaced the original hollow fiber (HF) membranes with reinforced HF membranes, which are more resistant to fat, oil, and grease (FOG) contamination. The new membranes also reduced fouling, which meant the system could go longer between cleanings.
Issues like inadequate mixing, floating aerators, and influent contaminants caused setbacks. For example, excess soap discharges from the laundry caused foaming and bacteria reduction. FOG discharges from the kitchen grease traps were worse —FOG sticks to the MBR membranes which clogs them to the point of needing replacement.
Veolia and the resort learned from these experiences and implemented design changes like reconfiguring tank layouts and installing above-ground blowers to lower power consumption and minimize hygiene risk to personnel. Procedural updates like grease trap inspections and staff training also prevented recurrences.
Built to last
MBR technology has created new efficiencies in wastewater treatment, intensifying treatment processes within confined footprints, lowering the total cost of ownership, and consistently producing high-quality effluent.
Nearly 20 years after its initial installation, the MBR system at the St. Thomas resort is still going strong. Here are some of the benefits that wastewater reuse has brought:
- Up to 80,000 gallons per day recycled for irrigation and toilet flushing
- No wastewater discharge to the environment
- Power consumption is roughly 10% of what it was for the previous, seawater reverse osmosis (SWRO) system
The resort’s wastewater reuse achievements demonstrate how existing infrastructure can be adapted for water recycling. With the right technology and operational changes, wastewater can become a resource rather than a waste.
A partner you can trust
Veolia has helped implement and optimize water reuse systems for clients worldwide and has decades of experience leading the way in developing new water solutions. Our team of experts will understand your unique challenges and find innovative ways to solve them. Contact us today to start or advance your water reuse journey.