
A European steam cracker plant was aiming to achieve a higher dilution steam production by reducing the oil quench column bottom viscosity and increasing the bottom temperature.
Viscosity of the quench oil is mainly affected by the presence of polymer and cokes. Coke particles come into the column with the cracked gas feed from the furnaces via the transfer line exchangers (TLE), while polymerization reactions take place as a result of the presence of unsaturated molecules.
High coke and/or polymer levels significantly increase viscosity, which affects fouling tendency in the oil quench coolers. This, in turn, reduces heat transfer through the unit, which affects dilution steam production capacity and increases both costs of production and maintenance.
In order to help meet the quench oil lower viscosity goal, Veolia recommended the use of a Petroflo dispersant which contains a hydrocarbon soluble blend of chain terminators designed to inhibit free radical polymerization fouling in the presence or absence of oxygen.
Superior performance in fouling control can be achieved by using a combination of inhibitors and dispersant technology, such as Petroflo. Veolia performed numerous analyses and laboratory test simulations to verify the treated and untreated viscosity values of the quench oil. Lab results obtained are shown in Figure 1.
A combination of a Veolia multifunctional antifoulant-antioxidant and a high temperature dispersant provided the best efficiency during the lab simulation tests. The treatment program was customized to inhibit polymerization induced with temperature and peroxides, decrease the catalytic activity of the soluble iron and help avoid agglomeration and deposition of particles.
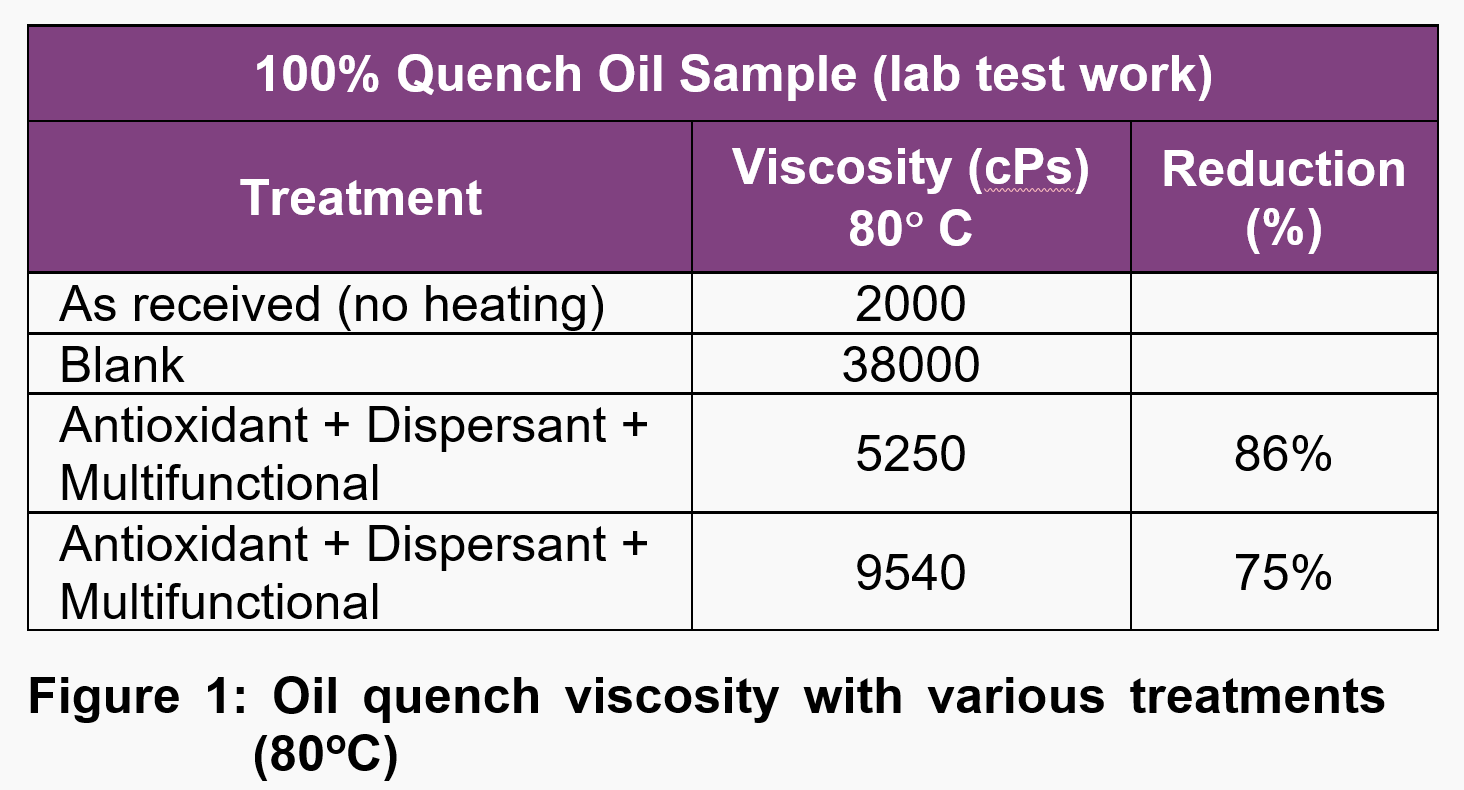
Result
Veolia used Multiple Regression Analysis (MRA modelling) to evaluate the treatment program’s impact on viscosity and dilution steam production. The comparison of the quench oil viscosity and the columns’ bottom temperature over a treated and prior untreated period clearly shows that the implementation of the Petroflo multifunctional antifoulant allowed the column to operate at a lower viscosity and a higher temperature (Figure 2).
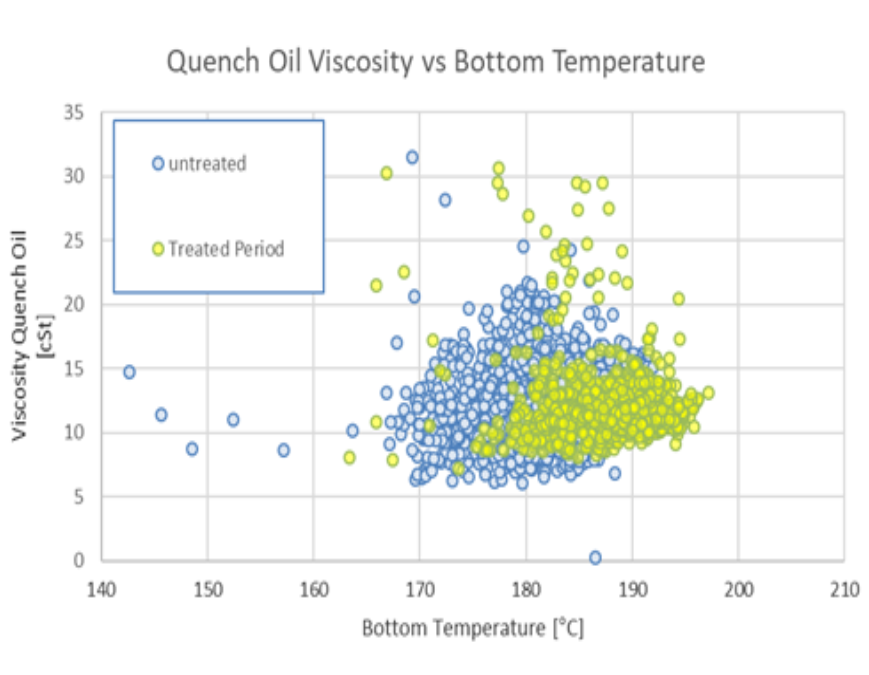
Figure 2: Quench oil viscosity vs bottom temperature (5 year run data)
Over the course of a treated run that lasted over 4 years, the measured vs expected bottom temperature, based on the effect of typically occurring fouling, showed a growing spread as measured temperatures remained stable. The reduction of the viscosity in the oil quench tower by Veolia’s antifoulant treatment prevented polymerization and maintained bottom temperature at peak production levels without requiring downtime or maintenance (Figure 3).
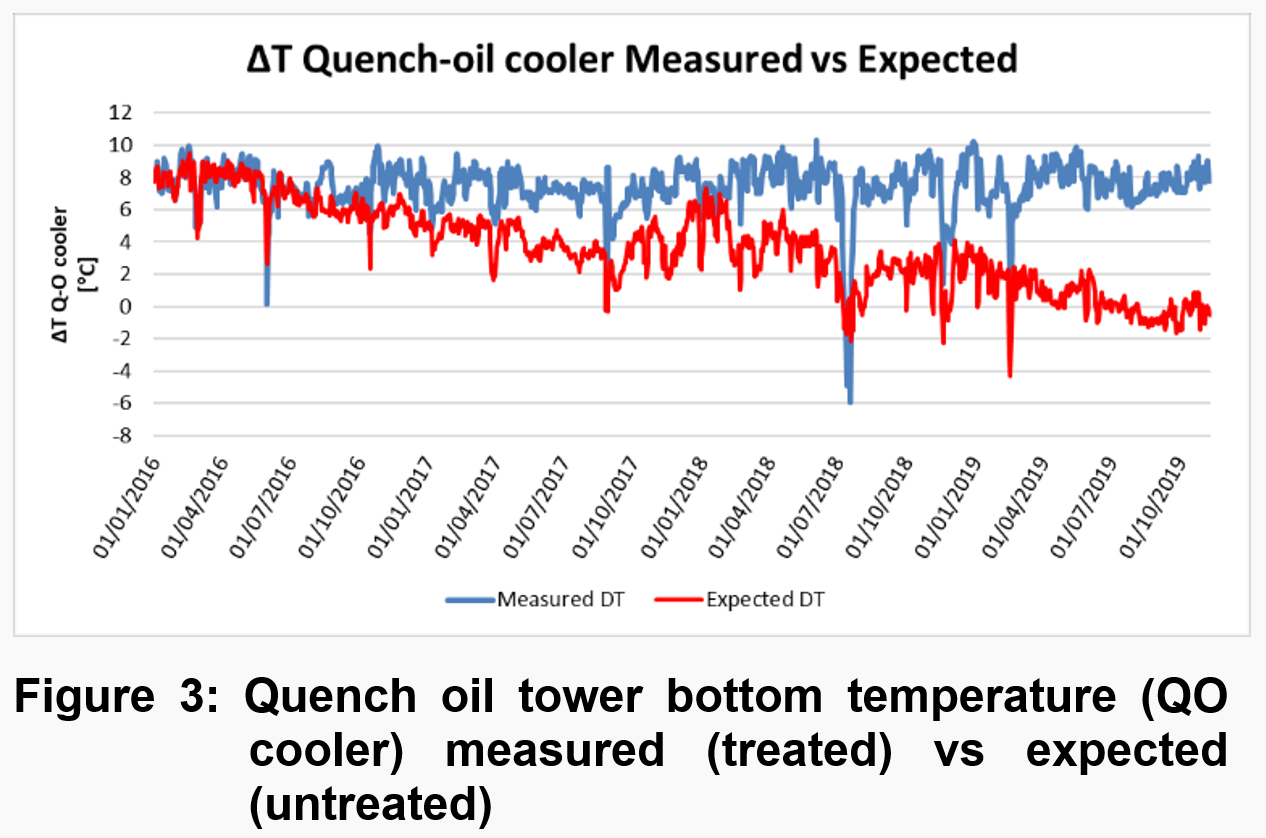
Over that 4-year operating run, the Veolia technology successfully controlled system fouling by decreasing the viscosity of the quench oil by approximately 5 - 10 cPs, which allowed to increase dilution steam production to 2.5 Ktons/month.
The value delivered by the Petroflo technology was recognized by the customer as highly impactful to their operation. The customer noticed several points of improvement in the unit, more particularly:
- Increased steam production and reduction of energy costs, valued at over $400,000
- Reduction in maintenance activities, cleaning costs and throughput limitation
- Estimated ROI > 400%