How Direct Lithium Conversion Simplifies Lithium Hydroxide Production
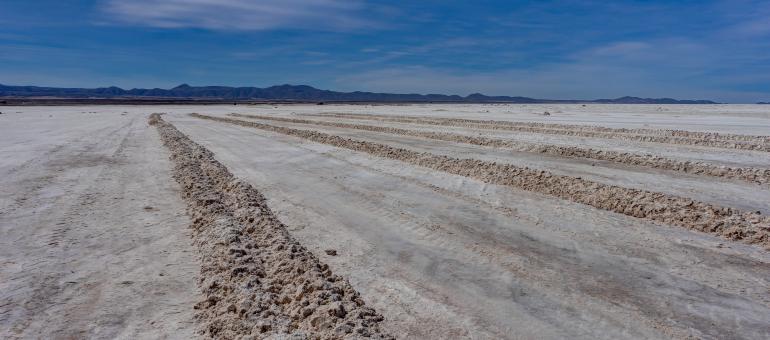
The global demand for lithium has tripled in the last five years, primarily driven by the needs of the battery manufacturing industry. As the world transitions toward cleaner energy sources and the adoption of electric vehicles increases, the need for lithium will continue to grow.
Lithium is a key component of electric-vehicle (EV) batteries. It is processed into either lithium hydroxide or lithium carbonate in the battery cathode manufacturing process. Lithium hydroxide is often preferred for battery chemistries incorporating nickel and cobalt. These batteries have higher energy densities compared to lithium iron phosphate chemistries which are more commonly used for EVs with a driving range of less than 300 miles.
Traditionally, lithium production has involved extracting the element from various sources, including hard rock, clays, and salar brines. Much work is being done to also extract lithium from produced water and geothermal brines. Once extracted, the lithium is then purified, concentrated, and ultimately converted to the form battery manufacturers can utilize in cathode production. The process of converting lithium chloride to lithium hydroxide is a multi-step approach that can be chemically-intensive and energy-intensive.
Conventional approaches such as using large evaporation ponds to concentrate the brine can face challenges and limitations, such as lower yields, reduced purity, and environmental concerns such as water loss.
A newer process called direct lithium extraction (DLE) is being developed because it replaces the dependence of evaporation ponds while also achieving higher lithium yields and faster processing than the traditional methods.
After extraction, the lithium needs to be converted to a usable form. To improve the method of converting lithium chloride to lithium hydroxide, Veolia Water Technologies & Solutions is developing a direct lithium conversion (DLC) process to simplify the approach to achieving a battery-grade lithium hydroxide product. DLC technology improves the efficiency and costs of lithium refining while also reducing environmental impact.
In the conventional method in converting lithium chloride brine to lithium hydroxide product, there is an initial conversion step of first producing a crude lithium carbonate product with the addition of sodium bicarbonate through a physical-chemical process. After the first conversion step to lithium carbonate, an additional step is applied to then convert the lithium carbonate to lithium hydroxide using another physical-chemical process with the addition of a hydroxide (usually calcium hydroxide). DLC technology replaces the conventional two step conversion approach into a single conversion step using a novel ion exchange process to directly convert lithium chloride to lithium hydroxide. This can greatly simplify process operations, while also reducing energy consumption, chemical usage, and waste generation.
How does DLC work?
Veolia’s direct lithium conversion process is a resin-based chemical process utilizing sodium hydroxide. It focuses on simplifying the transformation of lithium in aqueous brine solution to lithium hydroxide monohydrate, the product to be used for battery manufacturing.
After the lithium is extracted using DLE technology, pretreatment is first needed to remove divalent ions like calcium, magnesium, and sulfates. After the separation of divalent ions, the DLC technology utilizes a resin-based ion exchange process where lithium is captured on a resin and eluted with sodium hydroxide. The eluated brine from this ion exchange process becomes an aqueous lithium hydroxide solution, free of chlorides and other impurities such as boron. The lithium hydroxide solution is then concentrated by thermal technologies to evaporate out the water from the aqueous solution to reach supersaturation where lithium hydroxide monohydrate is crystallized and separated from the remaining aqueous solution.
Compared to traditional methods for producing lithium hydroxide, DLC technology streamlines the process to reduce the need for chemicals and reagents like soda ash and lime; this also results in fewer emissions than conventional methods.
Another compelling advantage of DLC technology is its cost savings. By simplifying the production process, reducing energy and chemical consumption, and increasing yields, DLC technology can significantly lower the overall cost of lithium hydroxide production. These cost savings can be passed on to battery manufacturers and ultimately to consumers, making electric vehicles and energy storage solutions more affordable and accessible.
As the world transitions toward a more sustainable future, the application of DLC technology as part of the overall flow sheet can help the lithium industry in the more cost effective production of lithium hydroxide monohydrate. By enabling more efficient and environmentally friendly lithium hydroxide production, DLC technology supports the growth of the electric vehicle and renewable energy sectors, contributing to the global effort to reduce carbon emissions and combat climate change.
Lithium Hydroxide and DLC in the lithium supply chain
With lithium demand steadily on the rise, securing a reliable and sustainable domestic supply of lithium becomes increasingly essential. The United States has traditionally relied heavily on imported lithium to meet its growing needs — relying on Argentina and Chile for 90% of its imported lithium from 2016 to 2019, according to the Department of Energy. However, this dependence on foreign sources leaves the country vulnerable to supply chain disruptions and price volatility.
America currently has only one active lithium mine, in Nevada, although others are in production. With $2.8 billion in grants from the Infrastructure Investment and Jobs Act earmarked for battery manufacturing and processing, the U.S. aims to reduce its reliance on imported lithium.
The development of DLC technology aligns with the government’s efforts to establish a more resilient and self-sufficient lithium supply chain. By embracing DLC technology, the United States can leverage its abundant lithium resources, such as those in the Smackover Formation in Arkansas, to create a robust domestic lithium production ecosystem. The adoption of DLC technology in the lithium supply chain benefits the United States and has global implications. As countries worldwide set ambitious targets for electric vehicle adoption and renewable energy deployment, DLC technology can help lithium producers more efficiently and sustainably meet growing lithium demand. Today, the traditional two-step conversion process is the proven and reliable way to produce sodium hydroxide. In many areas of industrial processing, Veolia is working on new technologies like DLC to move them towards commercial readiness.
Veolia leads the way in making lithium production efficient
Veolia’s DLC technology is best applied when co-developed with direction lithium extraction (DLE) technology providers. Proper consideration of recycle streams as part of the DLE technology can make overall projects more successful, improving yields and providing access to higher purity lithium hydroxide which is important in domesticating the country’s lithium supply.
As the world continues to embrace sustainable energy solutions, efficient lithium production is one of the most significant opportunities. Veolia has developed expertise in various regions, solving engineering challenges, optimizing operations, and creating an ecological transformation for customers.
Learn more about Veolia’s lithium processing abilities and contact our team to learn how DLC technology can improve your project and create higher lithium yields at the best purity standards.