How Grasim Industries Created a Zero Liquid Discharge Benchmark in Water-Scarce Nagda, India
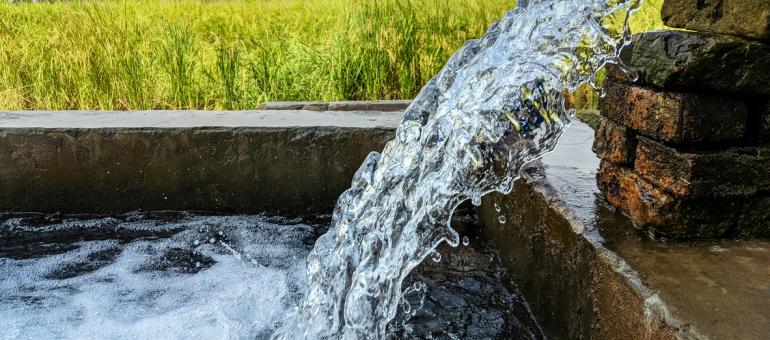
Water stress is an escalating issue in India, where nearly 70% of surface water is considered unfit for consumption and demand continues to outpace supply. In central India, seasonal droughts and inconsistent rainfall have placed even greater pressure on industrial operations that depend on stable water access. For manufacturers like Grasim Industries, this created an urgent need to rethink water use — not just to protect the business, but to safeguard shared community resources.
When Grasim Industries set out to revamp its water management strategy at its Nagda facility, it wasn’t just about keeping operations running — it was about setting a new global benchmark. Located in a drought-prone region of Madhya Pradesh, the viscose staple fiber (VSF) plant faced a growing challenge: rising water demand, unreliable supply and increasing pressure to reduce environmental impact.
Veolia helped turn that challenge into a model of industrial sustainability. Together, Grasim and Veolia implemented a first-of-its-kind zero liquid discharge (ZLD) system for the VSF industry, achieving a 98% recovery rate and cutting operational costs. Just as important, the plant now contributes recycled water and usable byproducts that support local communities, agriculture and the environment.
Grasim’s Nagda facility has operated since 1954. Water usage increased from 5.66 billion liters to 36.8 billion liters as the company expanded into sectors like cement, sponge iron and chemicals. Limited rainfall and reliance on the Chambal River pushed the plant to the edge, forcing shutdowns during peak summer months.
To break this cycle, Grasim focused on reducing its freshwater intake by adopting an aggressive strategy rooted in the principles of reduce, reuse and recycle. Membrane-based treatment, water storage capacity of 30 billion liters, and a commitment to UN SDG 6 helped transform the site into one of the world’s lowest water consumers in the VSF sector.
A clear set of goals
Grasim set out with a comprehensive set of water management goals: achieve ZLD compliance, reduce dependence on freshwater, recover valuable resources and create an energy-efficient, low-maintenance, highly automated system. It also needed to meet stringent quality benchmarks — including a treated water TDS level below 200 ppm — while minimizing its physical footprint and labor requirements.
In 2019, Grasim invited top-tier membrane technology providers to co-develop a new treatment system tailored for viscose effluent. Veolia’s deep experience in industrial water recycling, backed by a global track record, made it the clear choice.
“Although we contemplated handling the project internally, the learning curve and time constraints led us to prefer a globally reputed and established vendor. We didn’t want to go with untested players. Veolia’s track record with nearly 200 plants worldwide instilled confidence in our choice,” said Suresh Kodali, senior vice president of production at Grasim. “During the design phase, our experts and Veolia collaborated closely, addressing equipment construction, operating parameters, chemical usage, dosage patterns, recovery techniques and membrane selection. This collaboration resulted in the creation of a pioneering recycling plant, marking a significant milestone in our industry.”
Innovation that pays off
The plant’s recovery system centers on a multi-step process that includes Veolia’s patented clarifier, high-pH reverse osmosis (RO) and thermal treatment. These technologies work in tandem to treat and recycle nearly every drop of water on site.
One major innovation was handling sodium sulfate, a benign but abundant byproduct of viscose production. Rather than discarding it, Veolia and Grasim developed a system to extract and repurpose the salt for resale, creating a new revenue stream that offsets up to 50% of chemical production costs. The system also cut back significantly on energy use and eliminated acid feed, removing nearly 190,000 liters of acid annually while shrinking the site’s overall environmental footprint.
All told, the Nagda plant reduced water consumption by more than 75.7 million liters per year and achieved operational savings exceeding $100,000 annually.
Local and global impact
Grasim’s Nagda plant now recycles more than 98% of its water, supplies water for local agriculture and municipal use, and discharges almost nothing into the environment. The project has earned accolades, including the Golden Peacock Award for Sustainability in 2020, and is being considered a model for Grasim’s six other VSF plants. More broadly, the project highlights how industries facing water scarcity can partner with Veolia to deploy reliable, scalable solutions. With more than 25 ZLD projects completed across India and 500 installations nationwide, Veolia brings proven technology and hands-on support to help clients conserve water, reduce pollution and enhance operational efficiency.
Contact our specialists to learn how Veolia can help make your operations more sustainable, efficient and resilient.