YieldUp* Catalytic Coating Relieves Tube Fouling, Increasing Yield for Ethylene Producers
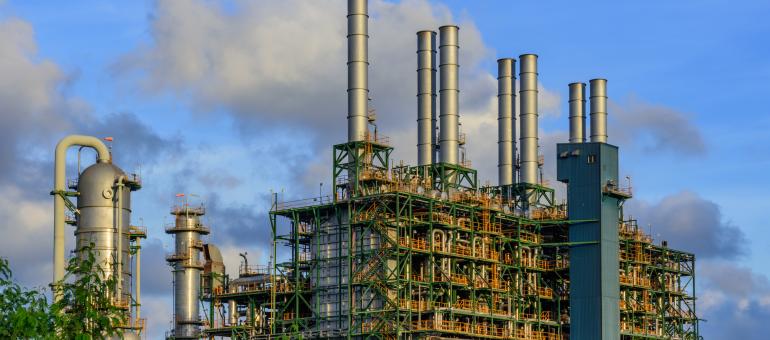
We’ve all faced high-pressure situations in our professional careers. But, when the stakes are highest – closing a big end-of-month sale, plugging a critical security vulnerability, or responding to a complaint or crisis – the pressure heats up.
Ethylene producers know a thing or two about pressure, especially those that utilize a steam-cracking furnace. It’s one of the most energy-intensive processes in the chemical industry and operating as efficiently as possible has always been challenging. With the global ethylene market expected to grow by 6% annually through 2030 - driven by rising demand for polyethylene for packaging, automobiles, and electronics, as well as technological advancements in bio-based production methods - operating efficiency is even more critical.
Consumer appetite for consumer-packaged goods products and their fast delivery continues to be a leading factor for ethylene demand. Additionally, ethylene is also used in the sterilization of medical and surgical devices and supplies, gas purification, and the production of unsaturated polyester resins, polyurethanes, solvents, antifreeze, and more. In addition, demand for ethylene will likely increase for Linear Low-density Polyethylene (LLDPE) in food and pharmaceutical packaging sectors because of its high tensile strength and puncture resistance.
With this much demand and growth potential, ethylene producers have a lot at stake. But, inside the steam cracking furnace is where the most pressure lives. Due to the vigorous heating in the hottest, radiant section of the furnace coil, which represents about 20-25% of all furnace coils, these radiant tubes are recoiled typically every 4-6 years. However, ethylene producers can save energy and reduce maintenance while extending tube lifetime and increasing yields with suitable coating for those coils.
Reducing Coke Buildup with a Thin Layer of Coating
The buildup of coke is common on furnace coils, and decoking must be performed roughly every 40 – 60 days. What’s more, the radiant tubes require recoiling and depending on the plant’s operations schedule, this take place every 4 – 6 years. Ethylene manufacturers can find new efficiencies by extending the life of these coils and extending the periods between maintenance.
In order to provide relief in such a pressurized environment, Veolia Water Technologies & Solutions developed patented technology, a 25-micron-thin soft catalytic coating – YieldUp – to apply to the inner surface of the radiant section furnace tube. Before the coating is used, the tube surface must be prepared and sintered at about 1,000 degrees Celsius in an inert atmosphere to build the microstructure and strengthen the coating’s adherence to the surface. This inert layer migrates into the chromia layer and functions as a catalyst to convert catalytic and pyrolytic coke to mainly carbon di-oxides.
Increased Efficiency, Higher Yields
Successful application of the YieldUp coating can double furnace run length from about 40 days up to 80 days, reducing the need to decoke as often and thereby increasing ethylene production capacity by 3% annually. Fewer decokes also translate to 4,000 MW in annual energy savings (for a midsize furnace -30 t/h) and a reduction in fuel consumption that cuts CO2 emissions by about 3% annually.
As more petrochemical operators utilize YieldUp, and we continue to define and prove the value of our catalytic coating for ethylene production, we remain committed to developing innovative solutions to relieve pressure in other applications. In addition, enhancing operations and the environmental footprint of ethylene production will make it possible to compete better and attract investors as market forces continue to drive up demand and urgency.
*Trademark of Veolia; May be registered in one or more countries.