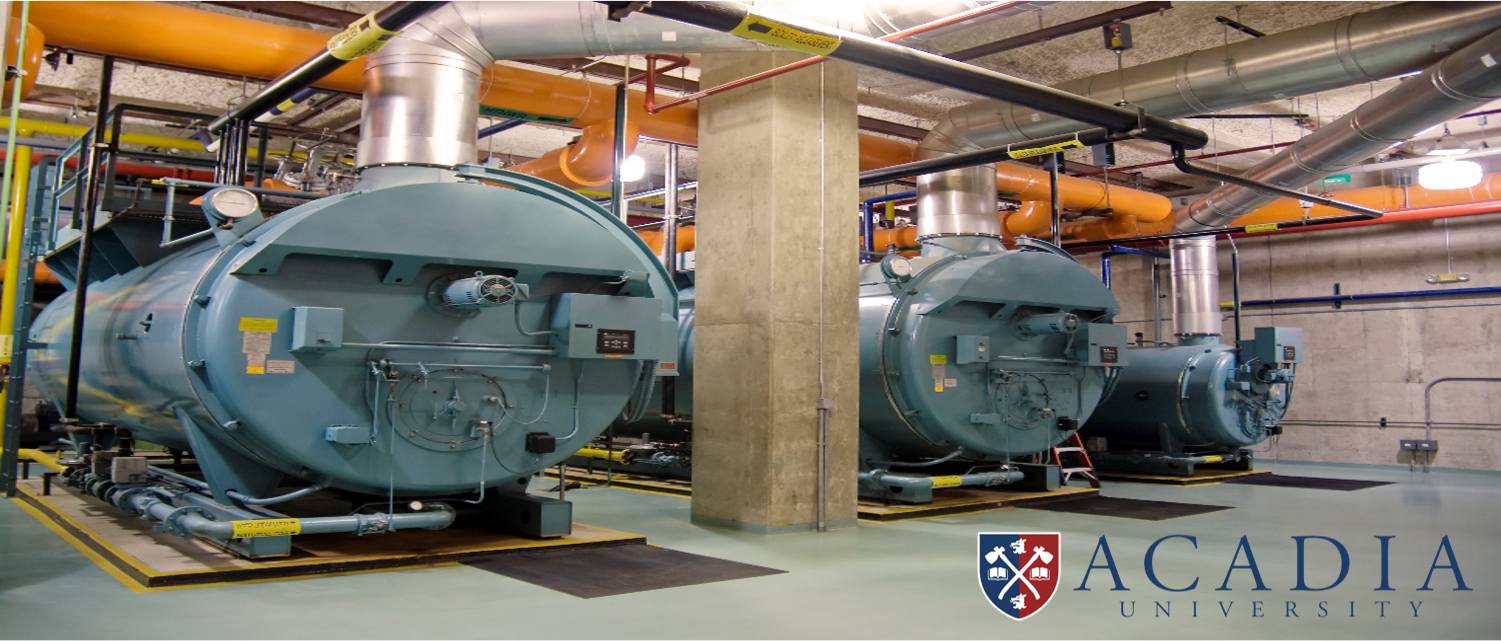

Challenge
The firetube boilers at Acadia University, in Nova Scotia, Canada, exhibited scaling on the boiler tubes during a boroscope inspection in 2013. This was due to medium-to-high concentrations of iron and hardness in the returning condensate for many years. The system is vast, scurrying underground across campus to connect the many buildings together. This makes it difficult to identify contamination sources in the system.
The boiler tube deposits were reducing heat transfer and increasing fuel cost, while also presenting a risk for the occurrence of under deposit corrosion and potential failures.
Although a common practice to remedy boiler deposits would be to conduct an offline acid cleaning, this procedure presents environmental and safety hazards, and can be quite costly. The university wanted to explore other avenues to improve boiler performance while preventing exposure of their team members to acid cleanings.
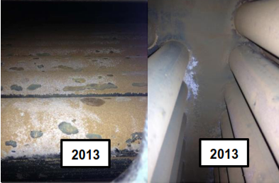
Solution
Veolia recommended the use of its novel Solus boiler dispersant. Solus is a third-generation boiler polymer that has a strong ability to prevent deposition of incoming contaminants and can dislodge long-time established deposits, without attacking the base metallurgy, unlike acids and chelants (ex: EDTA).
While the source of a contamination should always be identified and resolved whenever possible, the continuous of Solus would prevent further deposition and initiate a non-aggressive online cleaning of the boiler.
Result
Before the transition to Solus, the deposit on the boiler tubes at Acadia University were estimated to be 1/32’’ (mm) thick. Data published by the U.S. Department of Energy and the National Institute of Standards and Technology (NIST) indicates that a deposit comprised of calcium, magnesium and iron, of a thickness of 1/32’’ to 1/16’’ can reduce boiler efficiency by 3 to 5% 1.
After 3 years of applying the Solus treatment, another inspection demonstrated that the treatment was having great results, slowly removing the deposit layer on the tubes and leaving behind clean iron surfaces (Figure 2).
Inspections conducted in 2019, 2020 and 2022 further show the boiler tubes’ improving condition (Figure 3).
Based on a 3% heat transfer improvement, the energy savings to the university are estimated at 4 000 MMBTUs. This reduction in natural gas usage prevented the emission of 13 metric tons of CO2 and provided operational savings of 77 500$ per year.
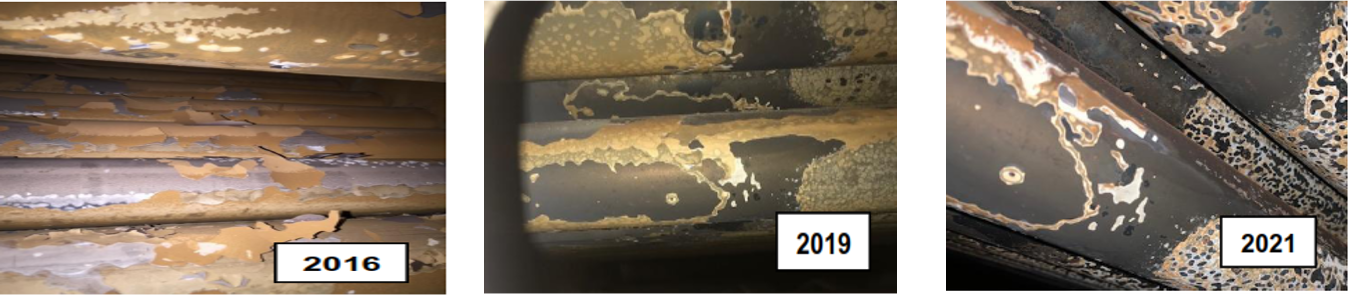