
Challenge
A leading Food & Beverage manufacturer producing ready-to-drink dairy and non-dairy products had a goal to achieve net zero greenhouse gas (GHG) emissions by 2050. The manufacturer operates a state-of-the-art production facility and distribution center in the Midwest and is dedicated to meet growing consumer demand of dairy beverages in America.
The product makeup of the plant is a combination of dairy and non-dairy products, and the wastewater produced by this facility is often discharged intermittently as tanks, homogenizers, heat exchangers, bottling lines, and other equipment are cleaned between production runs. Dairy wastewaters can be characterized by their high organic load, wide pH range, and increased temperatures. Due to the increased organic content, dairy wastewaters have high levels of chemical oxygen demand (COD) and biochemical oxygen demand (BOD), in addition to fats, oils & grease (FOG) and macronutrients such as nitrogen and phosphorus. Dairy effluents decompose rapidly and deplete the dissolved oxygen level of receiving streams so they can’t go untreated for long.
A wastewater treatment plant was installed by this manufacturer in 2007 during construction of their state-of-the-art production facility. At the time, the local publicly owned treatment works (POTW) had a common outfall and was permitted to discharge untreated/partially treated wastewater during surge conditions directly into the local river. As a company that prides themselves on environmental stewardship, the possibility of their highly organic effluent being discharged to the environment during a storm surge was not an acceptable solution.
Solution
Several treatment technologies were evaluated, and given the water reuse criteria, Membrane Bioreactor (MBR) technology was chosen because of its extremely high quality permeate that could meet the specification for re-use in the onsite cooling towers. When the project commenced in 2007, Veolia’s ZeeWeed* 500D hollow fibre membranes were chosen as the solution for the system.
The full-scale wastewater treatment plant (WWTP) was designed for an average flow of 1.5 MGD. A few years later, the standards for the cooling tower makeup became stricter so the facility took the additional step of adding a reclaim Reverse Osmosis (RO) system. This way, the plant could now offset as much as 50% of their cooling water demand through reuse.
Process Design Parameters – PFD (Biological Part)
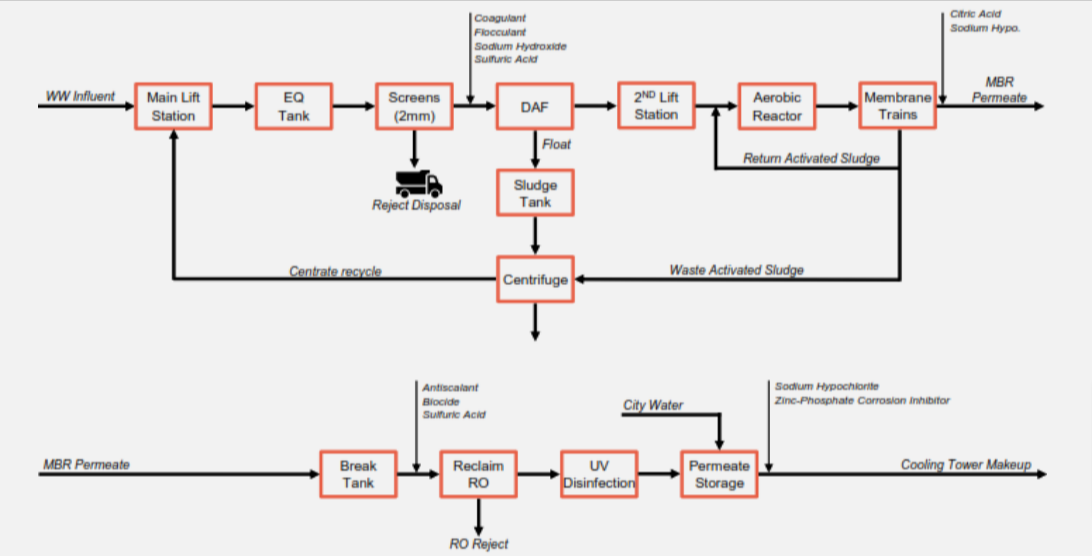
Process Overview
The WWTP consists of the following processes:
- Flow collection, pumping, equalization & screening
- Dissolved air floatation (DAF), sludge dewatering & bio-solids disposal
- Membrane Bioreactor (Activated sludge with ZeeWeed 500D ultrafiltration (UF) membranes)
Result
The beverage facility’s full-scale wastewater treatment plant treats an average daily flow of 1.5 MGD and the MBR system effectively removes organics, achieving 97.4% removal of BOD and 94.2% removal of COD from the process water (post DAF treatment). The ZeeWeed MBR also removes 95% of ammonia and produces a highquality effluent with a TSS < 1 mg/L suitable to feed the reclaim RO.
Up to 432,000 GPD of the ZeeWeed MBR permeate is further treated by a reclaim RO to reduce the TDS and produce high-quality reuse water for the plant’s cooling towers, chillers, and engine room. The reclaim RO can achieve a 98% removal of ions, which reduces conductivity from 1750 µS at the inlet to approximately 90 µS in the permeate.
The overall economic benefits of the reuse water at the plant include:
- A total annual reclaim water volume of 26.6MMUSG
- Reclaim water offset the total plant water demand by 31.6%
- Reclaim water (with 9% city water blended in) increased the cooling towers’ cycles of concentration before blowdown by 3
- The increased cycles of concentration reduced the annual water demand of the cooling towers by 9MMUSG or 11% in 2022.
The reclaim RO system provided a total annual water savings of 35.6MMUSG by both offsetting city water usage and reducing cooling tower water demand.
Veolia has continuous leadership in RO and MBR membrane solutions with our longest running membranes now more than 13 years continuous operation. If you would like to learn more about this process overview and our solutions for your wastewater treatment facility, visit us at our website.