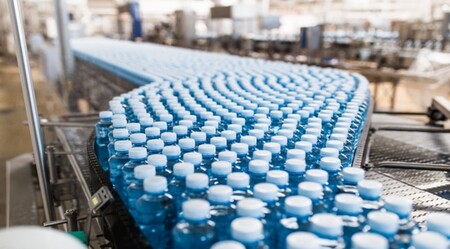
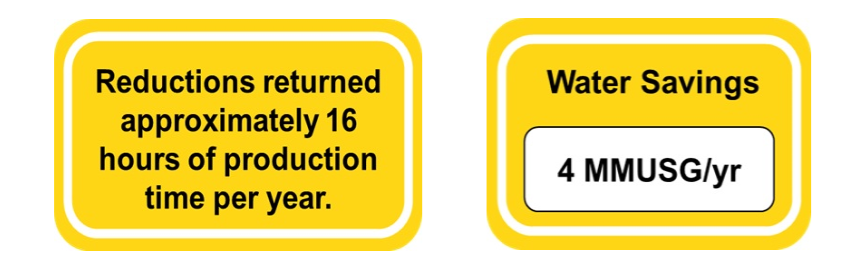
Challenge
A leading beverage manufacturers in the U.S is committed to responsible resource use and integrating sustainability into every aspect of their business. This includes driving water stewardship, energy efficiency, renewable energy generation and waste reduction, and continuously innovating to reduce their carbon footprint. As a fastgrowing company, they are constantly building new facilities or expanding facilities to meet product demand.
In 2021, they built a greenfield facility which produces purified water and must have less than 10 mg/L Total Dissolved Solids (and several other parameters). For the Reverse Osmosis (RO) system in this facility they needed a high-rejection RO membrane to achieve the plant’s needed purified water quality, but also mandated a highvolumetric recovery for the RO for their water-use-ratio and sustainability metrics. Another critical deliverable was minimal system downtime and operator interaction to maintain this high volumetric recovery.
Solution
Veolia Water Technologies & Solutions was selected to provide the high recovery RO system and the system was commissioned in 2022.
The RO system uses Veolia’s high rejection membrane elements which have an average ionic rejection of 99.8% to achieve the required purified water quality. This high ionic rejection puts more ions in the RO reject stream, and limits volumetric recovery.
The RO system operates at 93% volumetric recovery and was designed with an automated acid maintenance clean. This acid maintenance clean is impactful to the plant operation with:
- Minimized scale – removes mineral deposition on the membranes and keeps the system operating at peak recovery.
- Minimized downtime – plant production can continue during the maintenance cleaning process and the time between complete RO CIPs is extended which reduces downtime and lost production.
- Limited operator intervention – acid maintenance cleans can be fully automated and scheduled or manually initiated; thus limiting the need for operator decisions and operator time and effort. Also, by lengthening the time between full CIPs (fewer CIPs), less overall operator time is required.
Result
Since commissioning, the RO system has exceeded the recovery specifications for the customer.
The acid maintenance cleaning procedures permits the steady-state operation of the RO at 93% recovery (projected recovery without acid maintenance cleans is 90%). This will save approximately 4 million gallons of water per year. When the manufacturer increases capacity, water savings could increase to over 5 million gallons per year. In addition, extending the time between CIPs saves significant time and money for the manufacturer with every eliminated CIP reducing labor and chemicals and giving back approximately 16 hours of production time to the plant.