
Challenge
Steam condensate systems at colleges and universities can be large and complex, making them difficult to treat against corrosion and prevent leaks. The steam condensate piping system at the subject campus had been well treated over the years and was in good shape, but operation management knew that the average 50 ppb as Fe monitored regularly could be improved. That is because the steam plant is also a power cogeneration (cogen) plant, as it drives a 3.4 MW steam turbine with its 450 psig steam system. Due to historical turbine corrosion issues, a KPI (key performance indicator) for the institution was to protect the turbine and ensure its reliability, requiring that water and steam circulating in the system be of the outmost quality.
Additionally, due to the fact that the steam is also used across campus to humidify the air pushed through the heating and air conditioning (HVAC) systems in each building, the quality of the steam must be ensured and any chemical treatment used in the system must comply with OSHA and FDA guidelines for air humidification treatment.
Solution
In order to improve protection to the turbine and the overall condensate system, Veolia recommended the use of its novel FDA-compliant volatile filming technology, Steamate* VF1028. Filmer chemistry is not new to steam condensate treatment, as first generation filmers were in use over 50 years ago. But these products could be difficult to feed in the system and not volatile, so they had to be injected in the steam phase. For this reason, filmers fell out of favor to the profit of neutralizing amines.
In recent years, Veolia’s research and development work has enabled the release of new volatile filming chemistries, which alleviate the downsides of their predecessors. Volatile filmers can be fed much more easily to the boiler feedwater, carrying over with the steam throughout the system much more easily than early-generation filmers. Any returned condensate that contains residual filmer will contribute to system protection as it cycles again through the system, providing an additional benefit.
Result
The campus started feeding Steamate VF1028 in December. At that time, condensate iron levels monitored using Millipore filter tests showed approximately 40 ppb as Fe. The treatment was initiated at low dosage in order to prevent any upset or additional iron throw from a sudden chemistry change. Over the course of a few weeks, the dosage was increased incrementally up to the target dosage. After six months of treatment, as shown in Figure 1, iron levels were averaging 25 ppb as Fe, even though the condensate pH had typically been lower by at least 1 pH unit. The drop in pH was due to the reduction in neutralizing amine treatment dosage as the new volatile filming technology was introduced. Steamate VF1028 does not influence pH as its protection mechanism is based on the formation of a protective film on the metal surfaces, preventing corrosion reactions to occur between the water and the metal. The cost of the new filmer treatment program was comparable to the neutralizer-only historical program.
Metal surface samples were collected throughout the boiler and condensate system in multiple areas, and the presence of the filming chemistry was detected on all surfaces even though it is strictly fed to the boiler feedwater. This confirms the volatility of the novel filmer. All surfaces were also in great condition and exempt from viscous accumulation, which was another downside of previous generations of filmers.
The campus was extremely satisfied with the new and improved treatment now in place to protect its steam turbine and condensate piping, while also ensuring the steam met the required quality for air humidification with an FDA-compliant treatment.
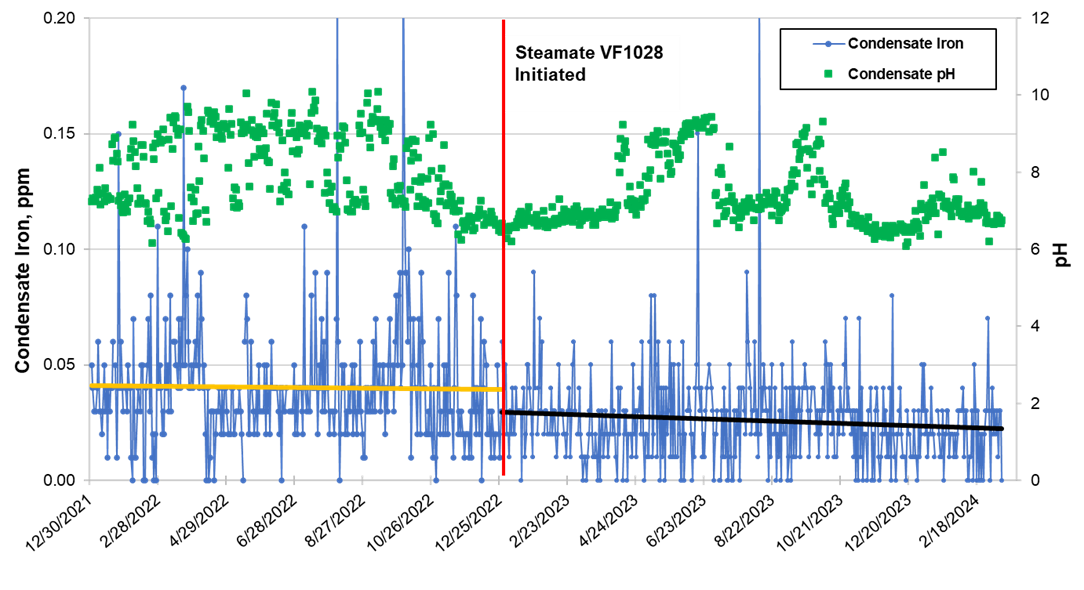
Figure 1: Progression of iron levels in condensate before and during Steamate VF1028 treatment, monitored with Millipore filter test