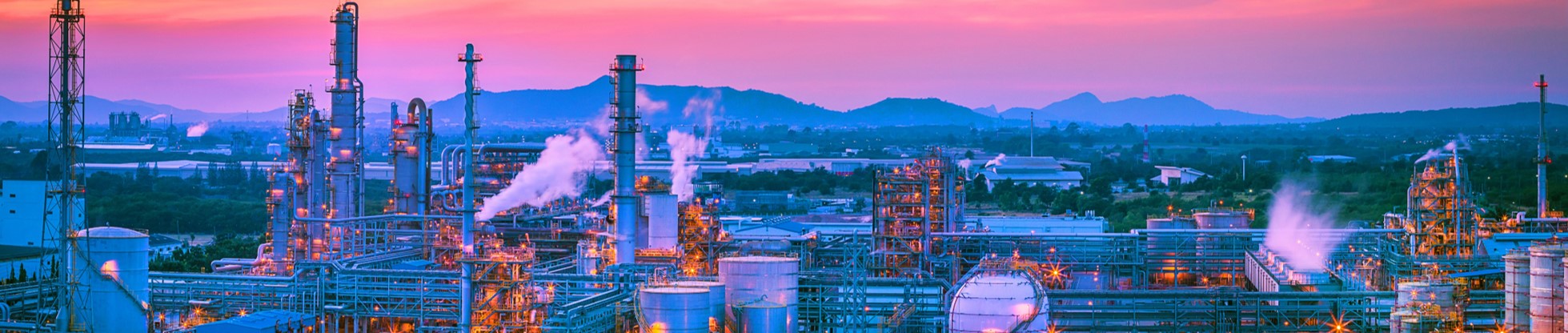

An in-situ Heavy Oil Production facility in Canada wanted to increase steam production through their existing Once Through Steam Generators (OTSGs) to increase oil production without increasing water plant throughput. The increased production would result in higher steam quality (steam/boiler water ratio), which would increase the total dissolved solids (TDS) content and pH in the OTSG boiler water.
There was a concern that the OTSGs would experience increased scaling due to the higher TDS present in the OTSGs’ boiler water at higher steam qualities.
To manage the risk of scaling the OTSGs, Veolia began a deposition monitoring program examining ion deposition rates in the boilers. This data was used to monitor the effectiveness of the chemical treatment programs used for the boilers, shown in Figure 2.
Veolia determined that relying on chelant alone for scale control would not be effective at the higher boiler pH’s and TDS loading, and proposed moving to a new dispersant focused program. A new boiler polymer designed by Veolia specifically for OTSGs was evaluated. Solus CL35 is a blend of chelant and patented terpolymer, which has been shown to be very effective in controlling scaling in comparison with industry standards.
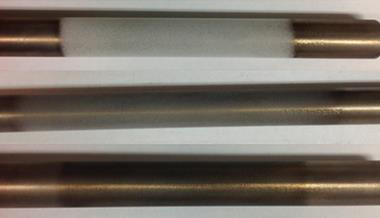
Figure 1 – Boiler probes treated with chelant only (top), a traditional homopolymer and chelant (middle), and Solus terpolymer and chelant (bottom).
Result
Program performance was verified by monitoring ion deposition rates across the steam generators. Figures 2 & 3 show the ion deposition rates before and after the chemical application, as well as the steam quality increase. From this chart, deposition rates remained steady or declined as steam quality and production was increased, indicating that the program was mitigating scale formation in highly stressed conditions. These analyses results agreed with the inspection data during the following planned outages.
This process change allowed for the customer to safely operate their steam generators at higher steam quality of 85% from the previous average of 74%, increasing productivity by over 10%. This led to an increase in steam production without increasing their water treatment plant throughput, saving over 14,000,000 USG per year of make-up water.
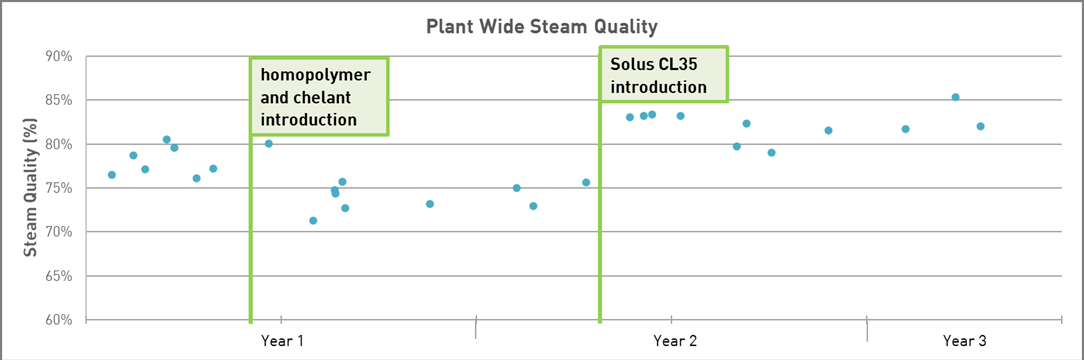
Figure 2 – Average Steam Quality from Once Through Steam Generators during an Evaluation of Internal Treatment Chemistries. Steam quality was safely increased, leading to increased oil production utilizing existing equipment.

Figure 3 – Hardness Deposition Rates from Once Through Steam Generators during an Evaluation of Passivation Chemical Treatment. Deposition rates improved through chemical changes and remained low as steam quality increased, leading to increased oil production utilizing existing equipment.