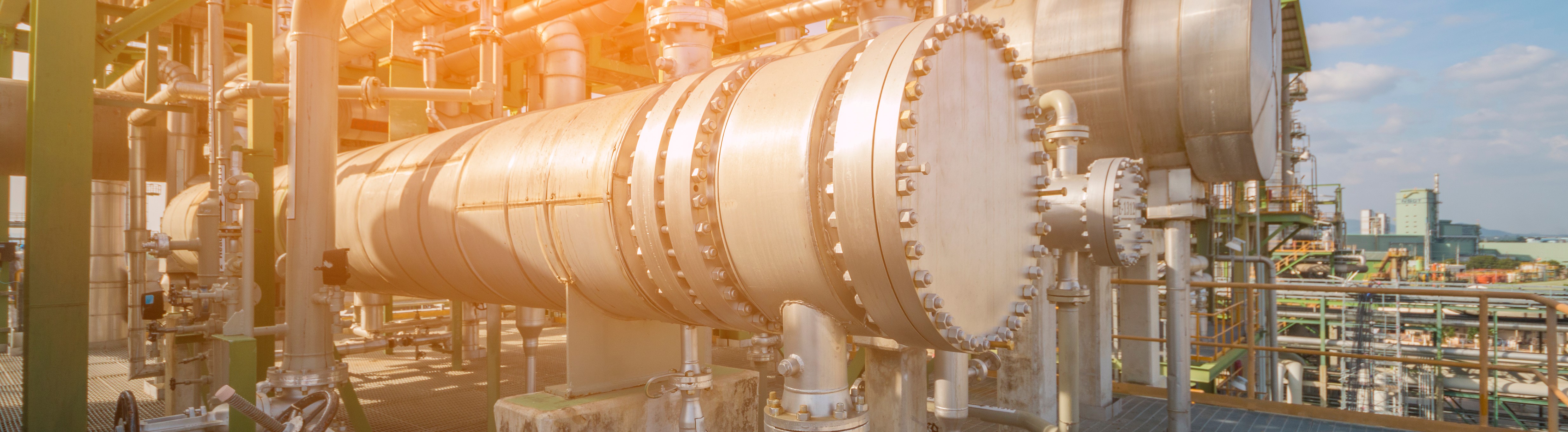
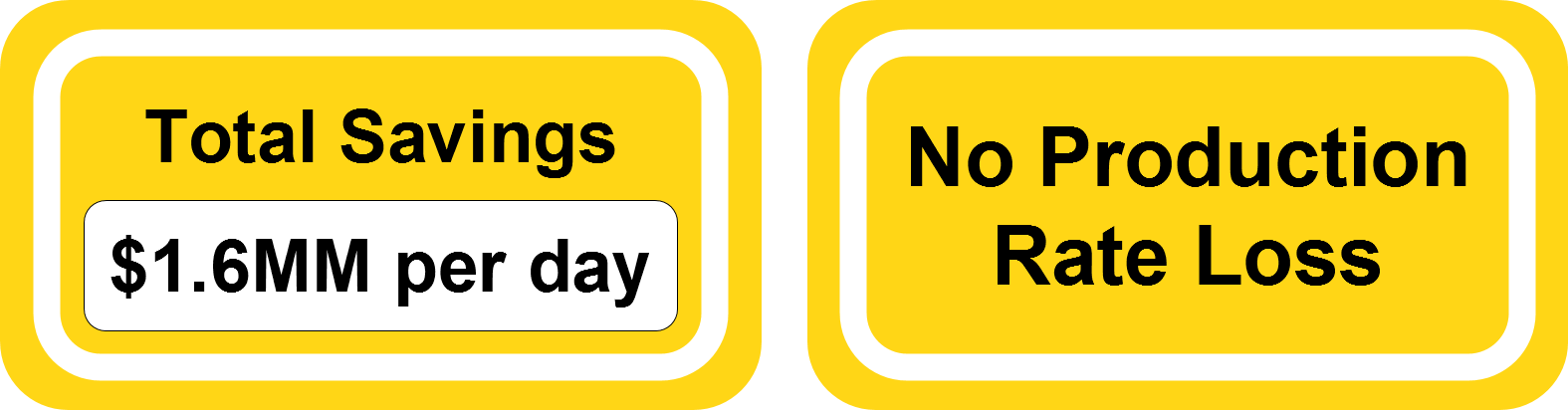
A Canadian oil upgrader was at risk of losing site-wide sour water processing capacity due to foaming tendency in the upper section of the concentrator tower. These foaming events would vary significantly, often related to contamination in the upstream coker sour water, and could cause operating difficulties.
In the absence of a treatment solution when these events occurred, the only option was to significantly reduce charge throughput of the upstream coker. In the past, a single foaming event required upstream coker processing rate be dropped by 42%, reducing production by as much as 50 KBPD (Figure 2). This event lasted 30 days and cost the plant $48MM, or $1.6MM per day.
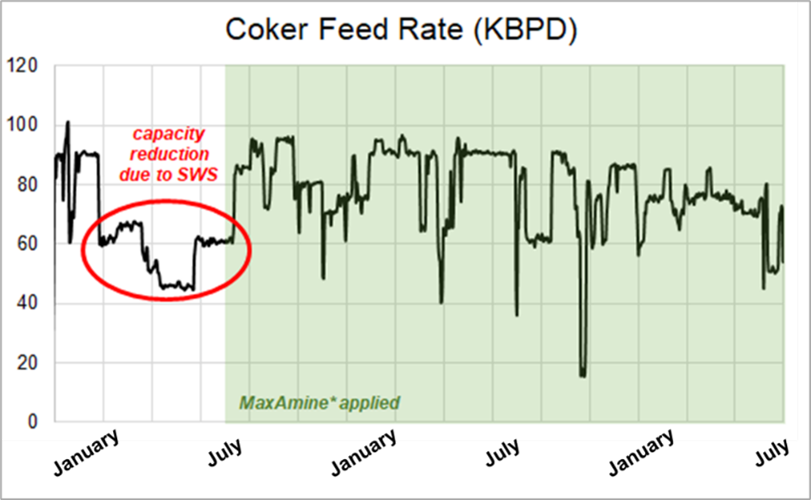
Figure 1. Coker processing feed rate with design capacity of 95 KBPD was reduced by 42% due to foaming.
The purpose of the sour water concentrator tower is to strip ammonia and hydrogen sulfide (H2S) out of the sour water streams generated throughout the upgrader site. The concentrator tower produces a stripped sour water product that may be recycled back in the process, as well as a concentrated waste liquid stream.
Aromatic hydrocarbons, such as naphtha, can be a major source of contamination in the concentrator sour water inlet stream, resulting in internal tower foaming. The foam acts as a physical “carrier”, resulting in liquid overflow into the concentrator overhead accumulator, thus limiting overall coker feedstock processing rate.
At this upgrader site, sour water from the upstream coker process was found to be regularly contaminated with aromatic hydrocarbons, resulting in significant foaming events and excess liquid overflow. The upgrader engineering team worked closely with Veolia to analyze the foaming issue and determine a solution that would mitigate risk of liquid carryover and coker throughput reduction.
Max-Amine, a specialty hydrocarbon antifoam chemistry, was selected as the best path forward as it provided an easy to use, online chemical solution to mitigate variable foaming events at the sour water concentrator without having to reduce coker processing rate.
Result
The antifoam application proved successful in reducing foaming in the sour water concentrator tower and provided the flexibility for the upgrader to run at maximum coker processing capacity.
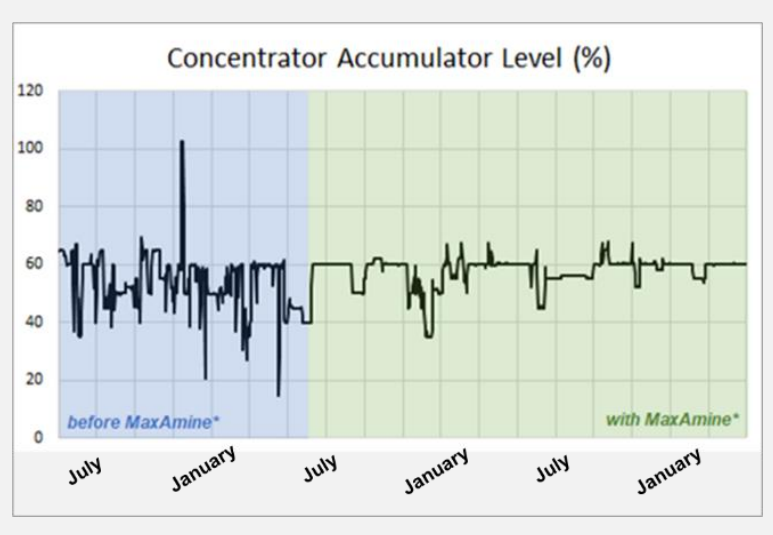
Figure 2. Concentrator overhead accumulator level before & after Max-Amine injection.
Veolia maintained excellent partnership with the upgrader’s operating team as the Max-Amine application stabilized sour water inventory level and prevented reduction of one coker’s processing rate. This prevented another sour water stripper outage similar to the previous one that had cost $48MM over 30 days, or $1.6M per day.
Overall, the antifoam Max-Amine application assisted in eliminating any production downtime and the need for re-routing sour water tankage volumes. The financial savings of the antifoam application for the customer were estimated to be $1.6 million a day in avoided production loss.