Frederickson Power Plant – Tacoma, Washington
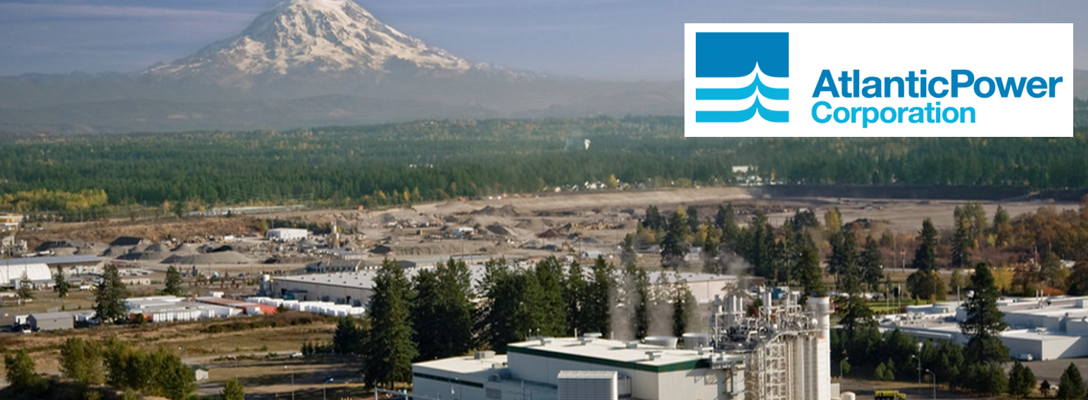
Many power plants operate in dispatch mode, supplying the grid on a day’s notice for a few days or weeks at a time. Unfortunately, this mode of operation implies that the steam generation system cycles “on” and “off” regularly, exposing critical assets to difficult conditions such as air intrusion and unstable water chemistry.
Cycling steam generators are especially susceptible to oxygen attack, acidic pH corrosion and FAC. These induce corrosion on the overall system, which has a severe impact on the plant’s reliability and represents a high cost in maintenance.
Challenge
Frederickson Power is a 250 MW Combined Cycle power plant operated by Atlantic Power in Washington state. Its generating system is comprised of a gas turbine sending its flue gas to a 3-drum heat recovery steam generator (HRSG), which drives a steam turbine.
The LP drum provides feedwater to the intermediate (IP) and high pressure (HP) drums, and the HP blowdown cascades to the IP. The boiler water treatment program includes phosphate (PO4) fed to the HP drum and a blend of ammonia/MEA for steam condensate treatment.
The plant averages 12 cold starts per year and can run from a few hours to a few weeks each time. The plant's main challenge is the downtime between each run, which can last as long as a couple of months.
Image 1 shows high iron levels were observed at start-up in the boiler system for many days, particularly in IP and HP drum, indicative that severe offline corrosion was taking place. The plant’s layup procedure included nitrogen blanketing, but the system could not be drained as it was required to be available to start on a day’s notice.
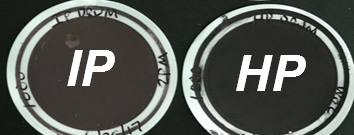
Image 1: Before Polyamine - drum iron Millipore samples after two days of operation show >10 ppm of iron
Base metal loss due to FAC was also confirmed in the LP evaporator by ultrasonic testing (UT) inspections. Based on UT thickness readings, Frederickson Power was repairing many tubes each year.
Solution
To mitigate its offline corrosion and FAC issues in its boiler system, Atlantic Power wanted to consider using a steam volatile film-forming treatment. Veolia recommended the use of its Polyamine technology in addition to the current boiler water treatment chemistry. Polyamine is a unique volatile filming technology that can provide strong protection against offline and online corrosion of boiler systems, both in the water and steam phase.
The trial's first phase was a 55-day period of operation where Polyamine was applied continuously to the boiler feedwater. The plant then went down for 70 days. On the following start-up, a reduction in iron levels was observed, although still high, especially in the severely affected areas of the IP and HP drums.
The second phase of the trial was 87 days of continuous treatment with Polyamine. Again, no operating or layup parameters were changed from the first trial or the historical operating practices. The following shutdown lasted 66 days, and when the plant came back online, a drastic reduction in iron could be seen in all sections of the system.
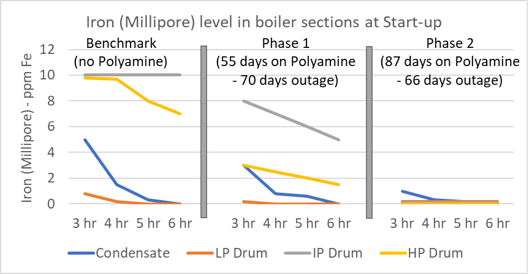
Image 2: Iron (Millipore) level in boiler sections at start-up (3-6 hours after start-up)
Figure 1 shows the progression of iron in the Condensate, LP, IP and HP drums before the initial trial and throughout Phase 1 and 2 of the trial.
Result
After a total of 142 days of application of Polyamine (Phase 1+2), the plant could see no iron throw in any of the drums 3 hours after start-up. This indicates that Polyamine successfully mitigated corrosion in all areas of the boiler and steam system. Image 2 and 3 show the After a total of 142 days of application of Polyamine (Phase 1+2), the plant could see no iron throw in any of the drums 3 hours after start-up. This indicates that Polyamine successfully mitigated corrosion in all areas of the boiler and steam system. Image 2 and 3 show the progression from the benchmark through Phase 1 and 2 of the trial at 3 hours after start-up for the IP and HP drums.
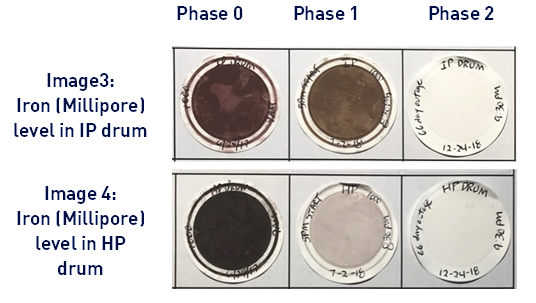
The benefit of the new Polyamine treatment has a positive impact on the operation and reliability of the plant, as stated by Joe Brooks, O&M Manager at the Frederickson Power Plant:
“Since we have implemented Polyamine treatment, the rate of FAC has reduced noticeably.”
Joe Brooks, O&M Manager
The pictures below were taken during a recent inspection after being offline for 66 days. The hydrophobic surfaces are seen across the system, including steam phase areas, and no corrosion was present even though the system was left full of water during shutdowns.
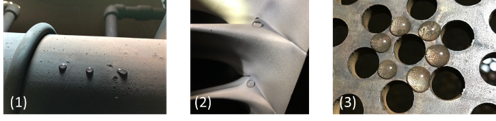
Picture 5: Hydrophobic surfaces at HP drum (1), steam turbine blades (2) and condensate hotwell screen (3)