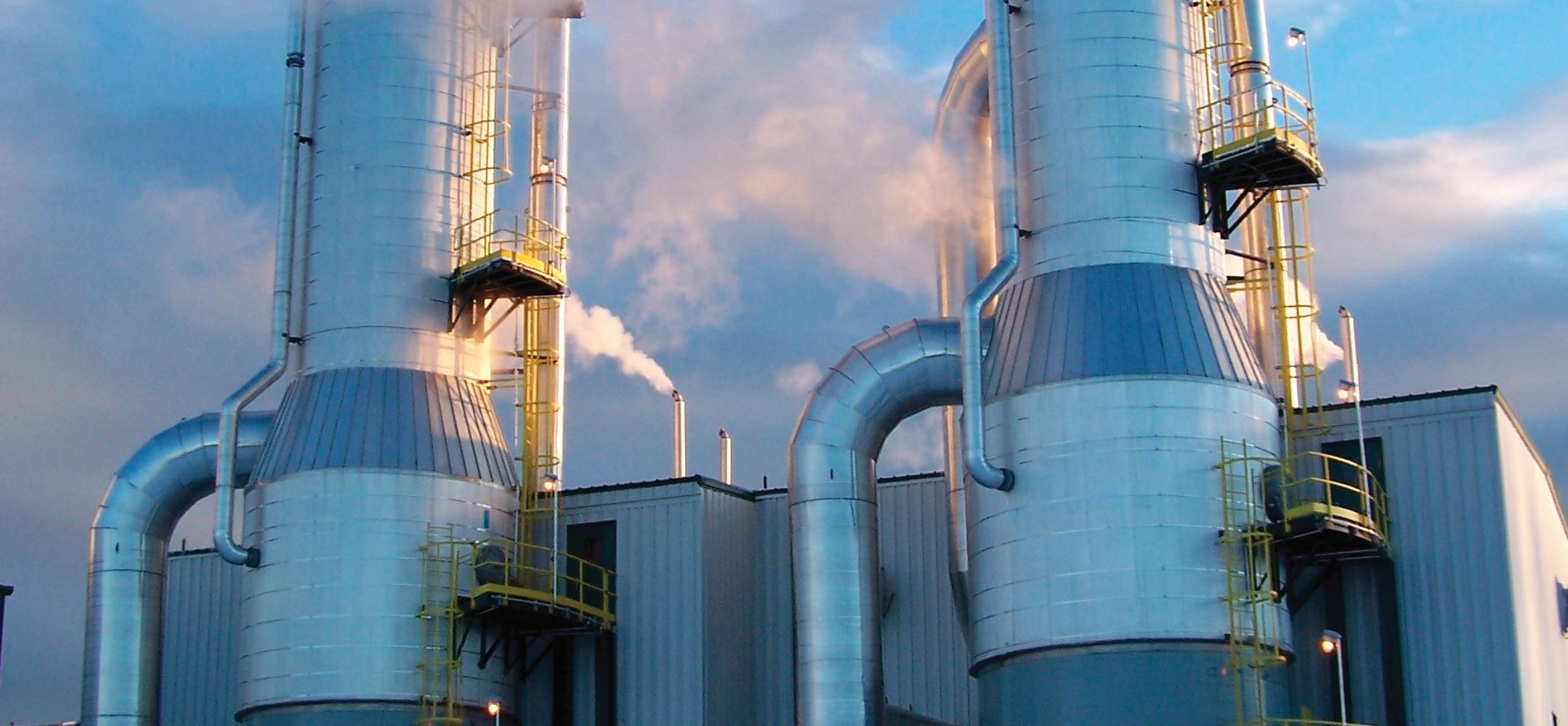

Challenge
An ethanol plant in the US Midwest was having to shut down every six months to hydroblast the evaporator system due to high pressure caused by evaporator fouling and original plant design constraints. The plant design, an original three evaporator system, did not allow for single evaporator CIP (clean-in-place) without having to stop production. The hydroblasting of the evaporator system every six months resulted in a loss of production of eight days per year and exposed workers to additional health and safety risk.
Solution
Veolia studied the evaporator system’s operational data from previous process runs and analyzed deposit samples to help determine what solutions to apply to drive down the fouling rate across the evaporator system. Veolia’s FoodPro* series offers a selection of specialty dispersants and deposit control additives designed to address organic and inorganic deposits. Some products can be used online, while others are designed for offline cleaning. FoodPro DCF online fouling control agents in combination with FoodPro OLC offline cleaners were carefully selected based on the data analyzed.
A baseline of system performance was established based on historical process data. A goal was set by the plant’s operating team in collaboration with Veolia to reach a 50% reduction in evaporator fouling rate by utilizing Veolia’s proprietary FoodPro additives.
While FoodPro DCF online treatment enabled longer runs between cleanings by reducing organic and inorganic fouling, steps were taken to obtain optimal cleanings when necessary. The plant installed bypass lines around each evaporator to allow individual CIP procedures and optimize the use of FoodPro OLC offline cleaners while minimizing impact on plant productivity.
Result
Following the implementation of the FoodPro DCF fouling control treatment, operational data showed that the rate of increase in pressure was significantly reduced on all subsequent process runs. As individual evaporators showed signs of fouling, targeted CIPs could now be applied strategically, which significantly reduced the number of CIPs as well as reducing the amount of water, caustic and other chemicals used.
From the decrease in pressure build-up across the units, it was determined that fouling rate was reduced by 91%. Because CIPs were now optimized and sufficient to reset evaporators to their design operating conditions, no hydroblasting had to be conducted in over 5 years.
The elimination of lost production days due to hydroblasting increased productivity of the plant by $1.5MM per year.
While the FoodPro treatment drastically reduced fouling rate by 91%, it also enabled the plant to run a higher solids content out of the evaporator system. Syrup solids content increased by an average of 18%. This increase in syrup solids reduced overall energy usage by ~10% on the dryer alone, delivering additional savings and reducing the carbon intensity of the operation.
Moreover, the elimination of hydroblasting prevented plant maintenance personnel exposure to hazardous conditions and eliminated water usage associated with this procedure.