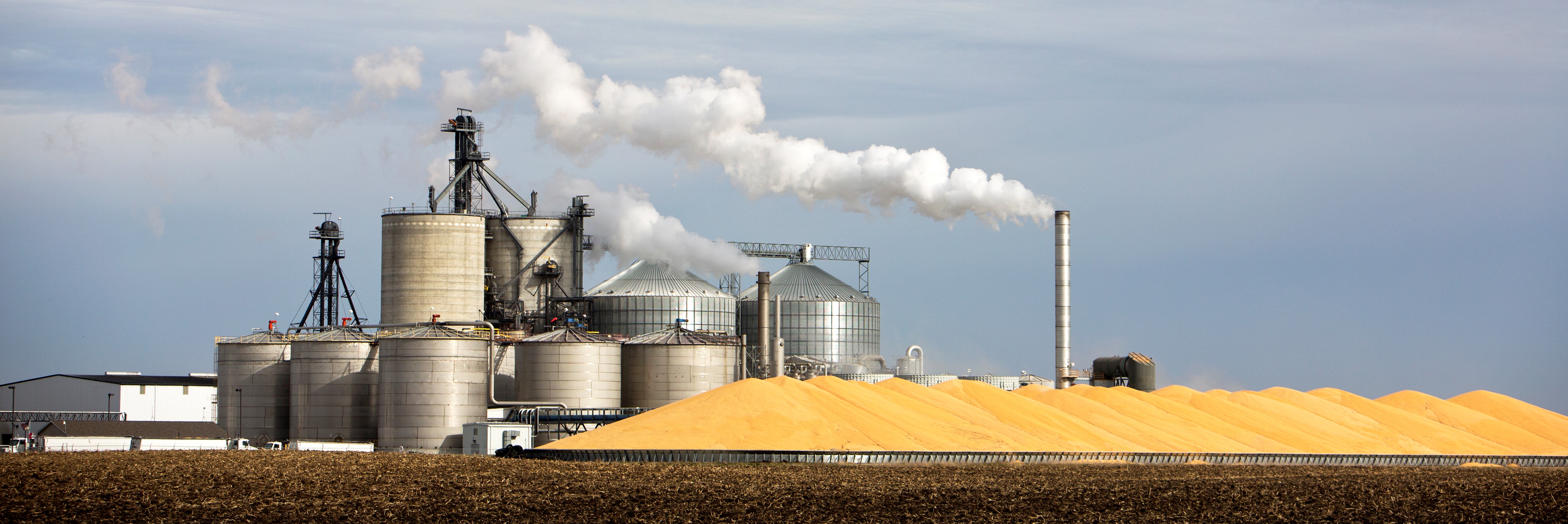

Although phosphorus (P) is an essential element to sustaining life, it also acts as a nutrient when discharged into the environment. The increased concentration of phosphorus in bodies of water leads to unnatural algae growth, upsetting indigenous fauna and flora and impairing biodiversity.
Many governments are implementing new regulations to limit phosphorus discharge into the environment. In the case of this ethanol plant, the state directed guideline was revised to <0.68 ppm as P. Their average phosphorus discharge concentration was 0.96 ppm as P, so the plant needed to review all sources of phosphorus to its effluent and determine where a reduction was possible without affecting the system's protection and reliability.
The facility was using phosphorus-based treatments for cooling tower mild steel corrosion control and reverse osmosis (RO) antiscalant. There are also trace concentrations of phosphorus in the well water.
As the cooling tower blowdown was the most significant source of phosphorus, the cooling treatment program was naturally targeted for phosphorus reduction.
Veolia recommended converting the phosphorus-based cooling tower treatment program to its new E.C.O.Film1 non-phosphorus2 and non-zinc treatment.
E.C.O.Film is a unique treatment technology developed by Veolia that generates a protective matrix which offers stronger protection against corrosion than traditional phosphate programs and does not represent comparable fouling potential.
1 E.C.O.Film = Engineered Carboxylate Oxide Film
2 May contains trace amounts
Result
After a year of treating its cooling towers with E.C.O.Film, the ethanol plant’s phosphorus discharge level averaged less than 0.25 ppm as P (see Figure 1), a reduction of 75% from previous levels, and lower than half of the new imposed limit of 0.68 ppm as P.
At the same time, it was important to ensure that the cooling system protection was maintained. The ethanol plant management was happy to see that the cooling system's protection was improved substantially through this treatment program change. While the previous treatment showed mild steel corrosion rates of ~2.4 mils per year (mpy), E.C.O.Film provided an average corrosion rate of 1.3 mpy; a corrosion rate reduction of 45% (see Figure 2). In addition, scale and deposit control, microbiological control, and overall asset protection and reliability have been excellent since implementing E.C.O.Film.
Improvements in piping and equipment life expectancy and environmental compliance were valued at over $140,000 per year.
Moreover, the reduction in phosphorus discharged to the local river, which amounts to a decrease of ~2.1 lb/day, is anticipated to lead to the prevention of up to 380,000 pounds of algae per year3.
Figure 1: Cooling tower phosphorous discharge level
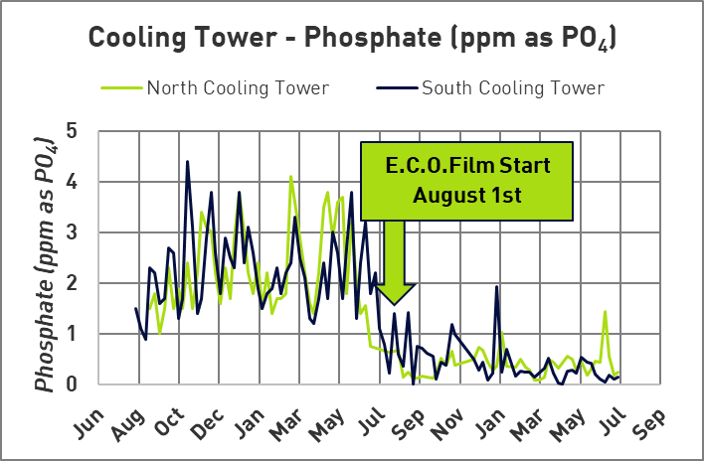
Figure 2: Cooling tower mild steel corrosion rates
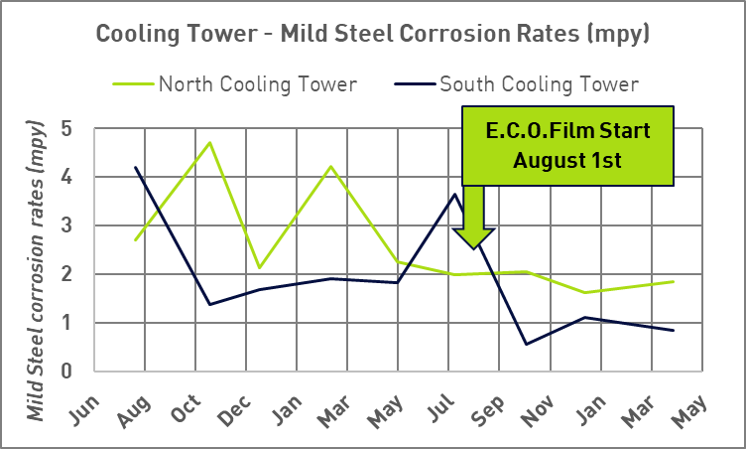
3 R. G. Wetzel, Limnology: Lake and River Ecosystems. Third Edition. San Diego (California): Academic Press, p. 275, May 2001