
Challenge
A food manufacturing plant in the United States pre-treated its wastewater with pH neutralization followed by dissolved air flotation (DAF) prior to discharge to a municipal water reclamation plant. With limited operator time available, the company had commissioned a new wastewater treatment plant with a chemical feed system incorporating a Veolia coagulant and flocculant under flow-paced automatic control. This was done knowing that the wastewater was highly variable in flow. However, it gradually became apparent that the suspended solids/turbidity and biological oxygen demand (BOD5) loadings were independently variable, so chemical demand varied independent of flow.
The variation made chemical control difficult, and although effluent quality remained within agreed discharge limits, treatment costs had risen significantly. This mainly occurred because the operator, who was only assigned part-time to the wastewater plant, found it more effective to set the dosage for the higher influent turbidities expected each day and leave it at that setting for extended periods. Thus, overdosing was common. Veolia was asked to suggest improvements to reduce chemical treatment costs.
Solution
Veolia and plant engineering personnel decided to evaluate the use of real-time turbidity monitoring and apply coagulant dosage control based on that data. Although this strategy has been used before in feedback mode for trimming dosages, it can lag between dosage and demand due to the equipment retention time.
The new turbidity analyzer was installed in the neutralization tank before the DAF, in feed-forward control mode, to minimize the response delay. All data were integrated into Veolia’s InSight asset performance management (APM) system for real-time online visibility to plant and Veolia personnel.
The Veolia technical representative conducted a series of field jar tests to develop the relationship between influent turbidity and KlarAid* coagulant demand. This relationship was used to program the control algorithm of Veolia’s PaceSetter* Platinum controller.
The turbidity analyzer was used to record benchmark data for six months. The controller was then put in “automatic” for a pilot phase over the following three months.
Result
The dosage and monitoring systems were installed in January, while the automated control was activated in June of that year. The dotted green lines show the average usage rate for the two periods:
- January to June (without automation) - coagulant dosage proportional to flow, without adjustment, based on the turbidity of influent
- June to October (with automation) - automated coagulant dosage based on both online influent turbidity and flow.
Figure 1 shows that the average KlarAid coagulant usage before automation was 36 gpd, which decreased to 20 gpd after implementation. This represents a 44.4% reduction in usage and thus treatment costs.
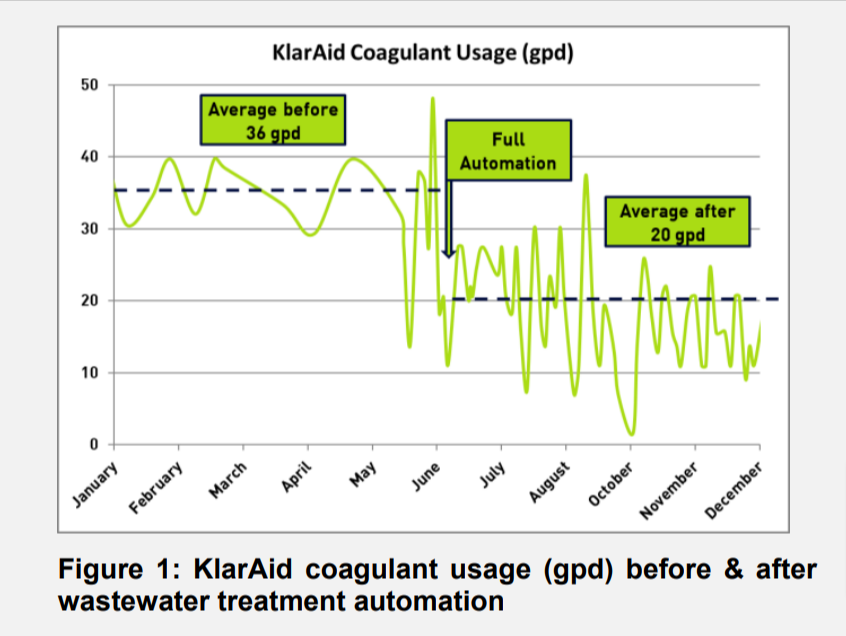
Effluent water quality also had to be assessed to determine the benefit of the automation. The key performance indicator for the plant was effluent BOD The agreement with the municipality limited the daily amount of BOD (pounds per day), with an agreed surcharge related to exceedances. Veolia tracked effluent COD routinely as an indicator of BOD, based on a previously determined relationship. Figure 2 compares the two periods of the trial and shows the average BOD at the discharge did not change significantly (~0.1% difference). The conclusion was that the reduced coagulant usage had no adverse impact on effluent quality and, thus, BOD surcharges.
The comprehensive automation solution provided by Veolia delivered annual chemical savings of over $100,000 with no loss in performance in the effluent treatment quality. InSight cloud-based asset performance management system allowed for monitoring of the system at all times, increasing the reliability of the operation.
This automation package is now available as a turnkey solution known as TrueSense* for Wastewater, which includes a turbidity analyzer, controller and InSight data management platform remote access.
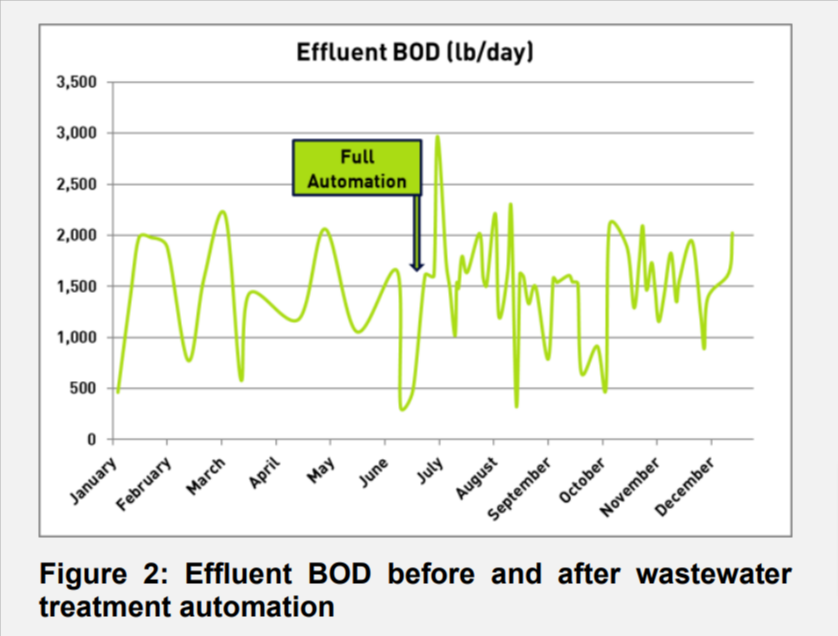