
Challenge
Pleasant Prairie Power Plant (P4) is one of the largest generating power plants in the State of Wisconsin, with an operating nameplate capacity of 1,190 MW. The plant traditionally operates in baseload, burning approximately five million tons of low-sulfur Western subbituminous (Powder River Basin) coal per year.
The plant has made significant investments in its Air Quality Control System (AQCS) to enable compliance with stringent regulations for particulate and gaseous pollutants, particularly nitrogen oxides and sulfur dioxide. These upgrades have included the addition of selective catalytic reduction (SCR) emission control units and Wet Flue Gas Desulfurization (WFGD) emission controls.
With air quality restrictions tightening, mercury has emerged as an area of concern for coal-fired power plants. Mercury is a toxic heavy metal that induces harmful effects in humans and organisms at very low concentrations. Upon combustion, mercury-containing coal produces three forms of the element that exit the furnace with the flue gas and enter the plant’s AQCS. Today’s AQCSs typically capture the majority of both particulate and oxidized mercury. Elemental mercury, however, is mostly emitted into the air with cleaned flue gas.
The extent to which mercury transits the AQCS and is emitted into the air depends on numerous factors, including coal composition, furnace/combustion conditions, combustion additives, flue gas temperatures, AQCSs in use, AQCS operations, and AQCS additives. Modifying these plant-specific factors can optimize mercury removal from the flue gas and decrease the emission of mercury into the environment.
To address mercury emissions, the plant added a bromide fuel additive to increase oxidation of elemental mercury within the flue gas. Upon combustion or introduction directly into hot flue gas, halogens produce oxidizing species that increase the oxidization of elemental mercury and improve the overall mercury capture in the existing AQCSs, primarily in the WFGD.
The halogen combined with the catalyst of the SCR provided sufficient mercury oxidation, but mercury reemission was documented, leading to periods of high mercury emissions. Re-emission occurs when the entering soluble oxidized mercury is captured within the WFGD slurry, but undergoes a reduction reaction that regenerates elemental mercury, which can then be released with the exiting flue gas.
Attempts were made to mitigate re-emission, including operational changes and scrubber additives. Operational changes lowered mercury, but not enough to satisfy the required limit. Carbon injection saw fair results but caused detrimental effects on the scrubber operation in the form of foaming. A scrubber chemical additive proved effective, but its cost was prohibitive.
P4 needed a solution that would allow them to continue to meet the U.S. Environmental Protection Agency’s Mercury and Air Toxics Standards (MATS) rule limits in a reliable and cost-effective manner.
Solution
Veolia proposed a new option to mitigate re-emission with the introduction of a FuelSolv* HG additive into the WFGD. A trial was conducted to determine to what level mercury could be controlled in the stack gas.
FuelSolv HG is an organic sulphide-based mercury reemission additive and can be fed at various points of the scrubber system. It precipitates mercury to ensure that oxidized mercury entering the FGD is dissolved within the alkaline slurry, partitioned to the solid phase, and unable to undergo reduction and re-emission. A stable, insoluble mercury polysulfide is formed that can be easily removed during solids separation.
Prior to the FuelSolv trial, the mercury emission rate was slowly increasing over a period of about six months (Figure 1). While still below the required limit, the trend clearly showed that respecting that limit would become ever more challenging and costly.
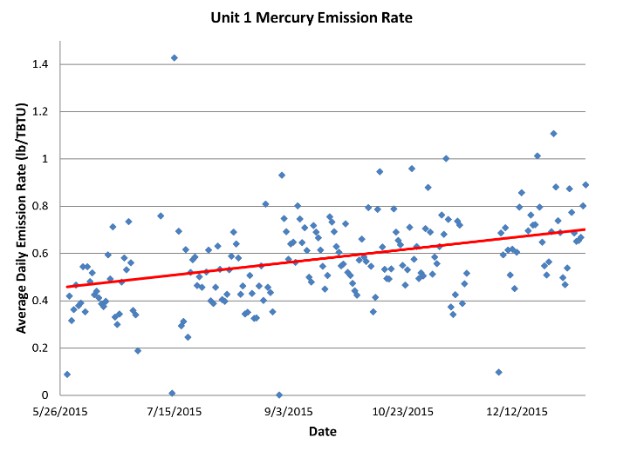
Figure 1: Before the addition of FuelSolv HG, the mercury emission rate displayed an increasing trend.
Product feed rate calculations indicated that a lower overall treatment cost would be achieved with FuelSolv HG. The incumbent treatment’s feed rate required to maintain mercury below the permitted limit was 2-2.3 gallons per hour (gph) on both power block FGD scrubbers.
The FuelSolv trial on unit 1 at P4 started with a conservative initial feed rate of 2.3 gph. Mercury emission appeared relatively stable after 24 hours so the feed rate was reduced to 2.0 gph. While carefully observing the mercury emission level, the feed rate was reduced by 0.2 gph on a bi-weekly basis. The rate was held steady for roughly two weeks at each set point to allow the low-purge rate scrubber unit to adjust to the treatment level.
A feed rate of 1.8 gph maintained stack emission mercury at a level equal to or better than before the trial. When this was achieved, the Unit 2 scrubber was changed over to FuelSolv HG at an identical feed rate.
Result
After a few months of steady operation and decreasing mercury emission rates, chemical feed rates to both scrubbers were decreased to 1.2 gph, always with careful continuous monitoring of the emission rate.
Figure 2 shows the summary emission data for P4 unit 1, clearly indicating the point when the chemistry was changed near the beginning of 2016. Since that time, and with a decreasing chemical feed rate, the mercury emission has continued to decrease.
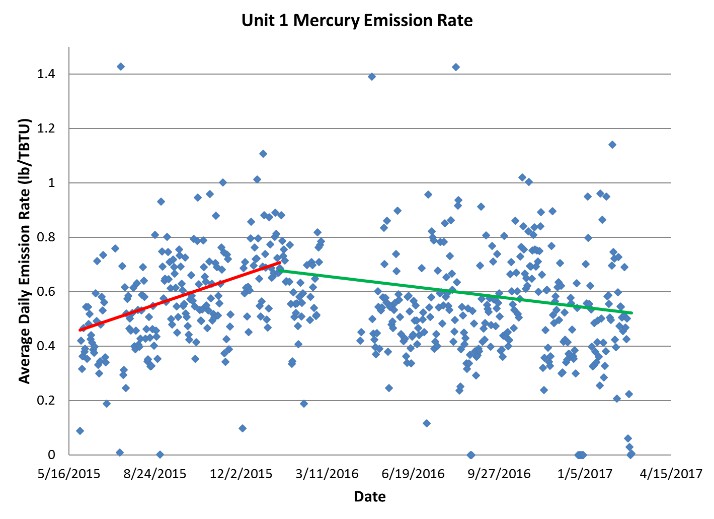
Figure 2: Comparison of unit 1 mercury emission data, including pre- and post- FuelSolv HG trendlines.
With FuelSolv HG, P4 has reduced its mercury emissions by approximately 65 percent compared to bromide injection alone. This equates to a 119-pound reduction in annual emissions and a savings of $100,000 per year.