Challenge
An Asian gas field producing large volumes of natural gas had significant levels of both hydrogen sulfide (>6%) and carbon dioxide (>4%), as well as free water within the gas. The risk of corrosion was considered to be high between the well heads and the gas purifying plant. There was evidence from operations in an alternative block which was processing the same gas that there had been sulfur deposition and subsequent under-deposit corrosion in the pipeline, predominantly in the bottom of the pipe.
Considering the expected life span of the gas field, a metallurgical upgrade was uneconomical.
A safe operation was a key goal, and the following corrosion abatement strategy would be implemented to achieve this goal:
(i) A thicker than usual schedule (L360) steel pipe would be specified;
(ii) A chemical corrosion inhibition program would be utilized.
- Multiple corrosion monitoring technologies would be employed to monitor corrosion, including: Electrical Resistance (ER) probe
- Corrosion Coupons
- Field Signature Method (FSM)
- Ultrasonic Thickness (UT) measurements
The operator of the gas field requested Veolia to study the corrosion potential and put forward a proposal for a chemical corrosion inhibition program suitable for the system as part of the design process.
Solution
Veolia prepared a recommendation by considering the following factors:
- Projected analysis of the produced water;
- Simulated corrosion laboratory studies. Both batch and continuous treatments were considered as part of the study;
- Referenced “Lessons Learned” from other gas pipeline corrosion applications.
Veolia recommended a program that specified the use of a Veolia pHilmPLUS corrosion inhibitor that was most applicable to this particular system. The pipeline operator adopted the Veolia recommendations and thereafter commissioned the program.
Result
A formal review of the Veolia corrosion inhibition program was made after 2.5 years of operations. The Veolia program was found to have successfully delivered the corrosion control target the pipeline operator had specified, which was 0.075 mm/yr. (3 (mpy).
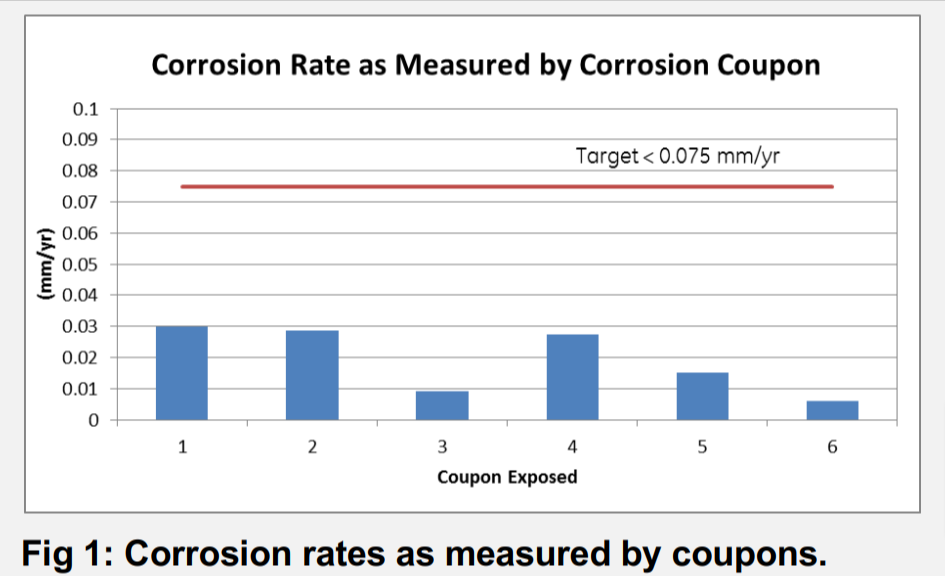
Each coupon period was typically three months in duration.
The appearance of the coupon showed only surface blemishing - there was no evidence of persistent under-deposit corrosion. In a similar location to the coupons over the same time period, the ER probe readings were recorded and showed similar readings to the coupon analysis results. The corrosion rate had also been controlled to below 0.055mm/s (2mpy).
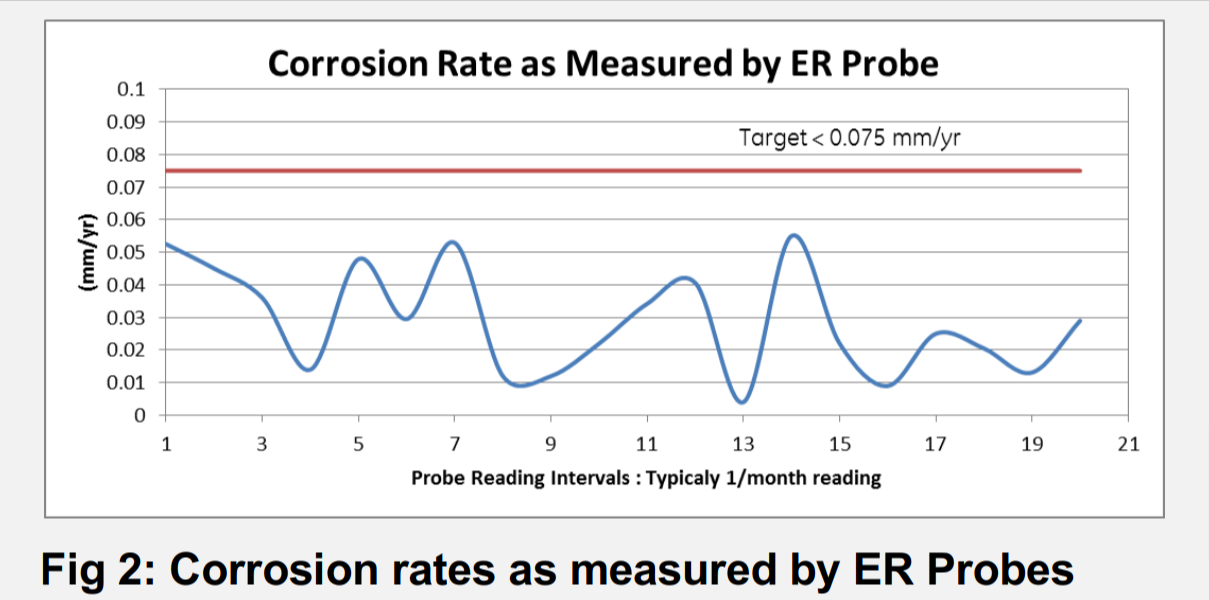
FSM were installed in multiple locations on the pipeline. Fig. 3 shows the corrosion rate from a typical location was measured at 0.5mm/s (1.8mpy).
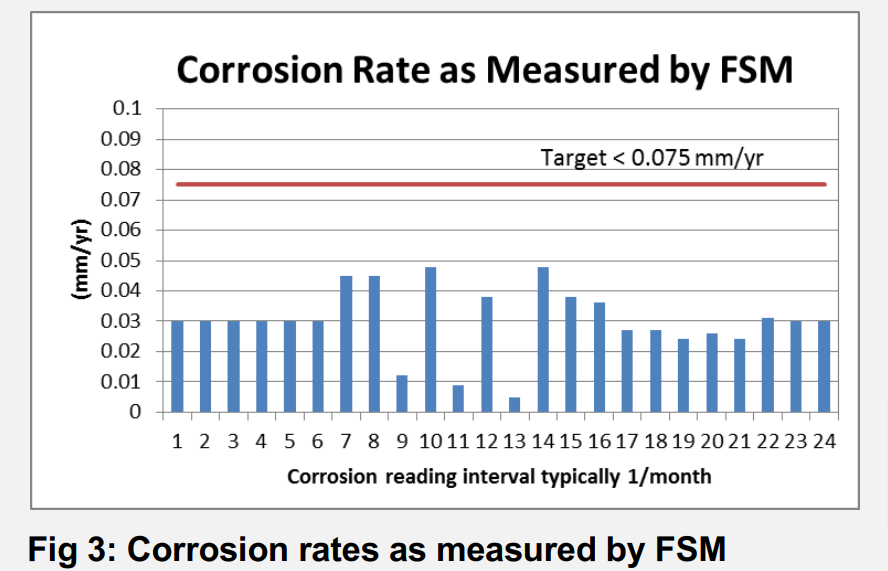
After considering the results of the three corrosion measurement techniques, it was concluded that the corrosion in the whole system was controlled below the target of 0.075 mm/yr. (3 mpy), and the assets in this gas field had been protected as expected.
Veolia analyzed any sludge that was removed from the system periodically. This provided additional information that allowed Veolia to make intermediate recommendations around the dosing of the chemical to optimize the results, especially around the chemical treatment in conjunction with pigging operations.
The great majority of all samples showed them to be predominately organic in nature, with only trace elements of corrosion product, further indicating positive corrosion control measures.
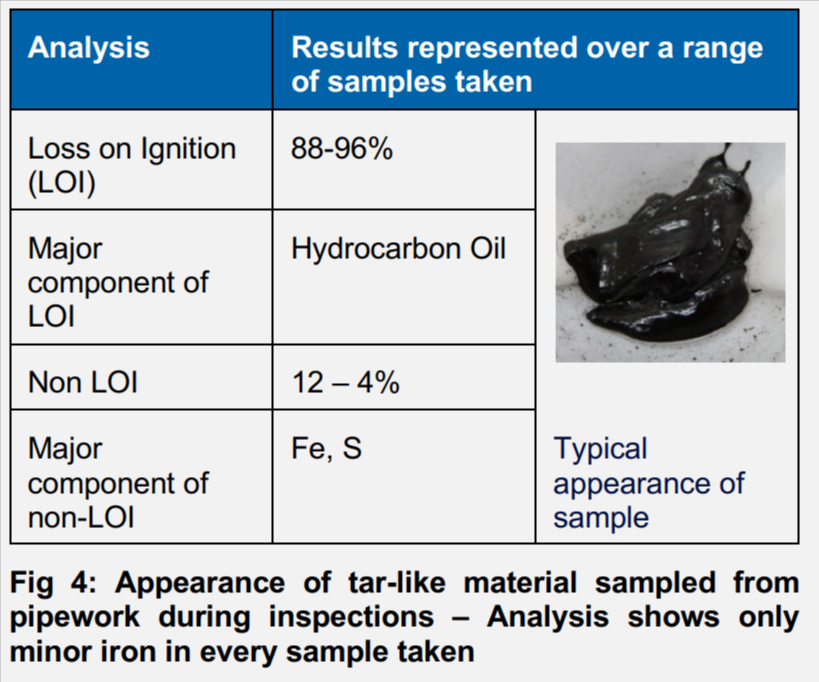
The program was also verified at the gas stations by a program of both UT measurements and visual inspection. The UT measurements showed no obvious thickness reduction. The stations were sequentially shutdown at 15-month intervals for maintenance operations, providing the opportunity for visual inspections. The inspections revealed that the equipment had been well protected.
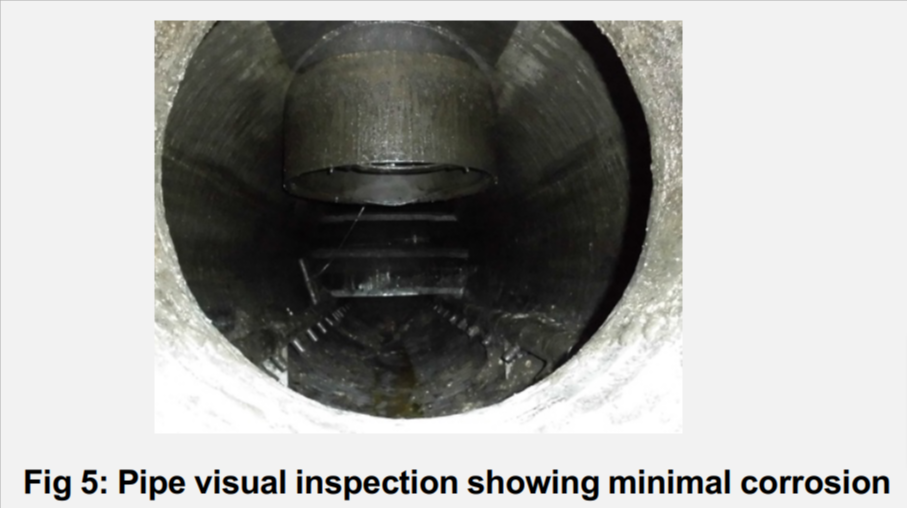
Smart pigging was also executed on the pipeline between each station at one-year intervals. Smart pigging is the insertion of a “smart pig” that can measure the wall thickness of the pipeline from inside the pipe across the entire run of pipeline. It is inserted into the pipe after a cleaning pig is used to remove any debris in the line. These results also showed minimal corrosion of the pipeline.
It was determined in the design stage of the pipeline that the wet sour environment of the pipeline Represented a significant risk of corrosion. The implementation of the Veolia corrosion inhibition program was successful in reducing the corrosion compared to other similar pipelines operations, yielding safe and environmentally-sound operations.