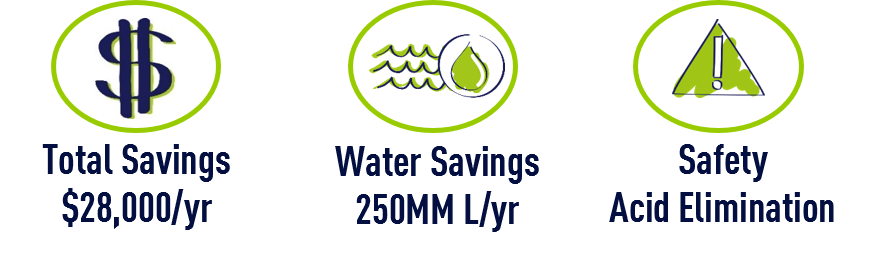
The cooling tower at this integrated steel mill required high acid and excessive blowdown to prevent deposition. This was leading to high operating costs and excessive freshwater consumption.
Veolia recommended the use of GenGard, which uses a unique dispersant technology. The efficiency of scale prevention allowed the plant to eliminate the acid feed and doubled the tower’s cycles of concentration, saving 250MM liters of water per year.
Cooling towers operate on the principle of evaporation. The warm water that trickles down the tower dissipates heat by evaporating a portion of the water. The water which doesn’t evaporate reaches the tower sump at a much cooler temperature and can be sent back through the cooling system. The water lost through evaporation must be replenished with make-up water to maintain the system level.
The water that evaporates only contains H2O but has none of the dissolved salts found in the cooling water that is provided by the make-up. As this cycle is repeated, the salts concentrate in the cooling water. Concentration is controlled by blowing down a portion of the cooling water to the effluent. The ratio of salt concentration in the tower to the amount found in the make-up is referred to as “cycles of concentration.”
Cooling tower efficiency relies on the ability to concentrate salts without exceeding their solubility threshold. Concentration ensures water conservation and chemical savings, but over-concentration forms precipitate that will scale heat exchangers, reducing heat transfer and productivity, leading to costly outages and maintenance.
A fully integrated Canadian steel mill runs a secondary non-contact cooling tower that provides cooling to the plant’s closed loop heat exchangers.
To mitigate deposit issues caused by calcium and phosphate, the steel mill was feeding acid to depress pH but still had to reduce cycles of concentration to only two. This mode of operation was generating an excessive amount of blowdown water and was sending a lot of treatment chemicals to the drain.
Veolia moved on site and implemented its GenGard technology, an exclusive treatment program designed to allow systems to safely handle a high load of contaminants in alkaline conditions. GenGard combines a stress-tolerant polymer (STP), alkaline enhanced chemistry (AEC) and halogen resistant azole (HRA) with phosphate-based steel corrosion inhibitors.
The GenGard program allows cooling towers to operate with a much higher residual of calcium and phosphate safely and effectively. The STP and AEC polymers keep the calcium and phosphate in solution, greatly reducing the risk of forming deposits. Veolia recommended that the tower operates at four cycles of concentration without the addition of acid for pH depression.
Result
Increasing the system’s cycles from two to four significantly reduced the amount of water discharged by blowdown and saved an equal amount in fresh water. These water savings amounted to over 250MM liters per year, a reduction of 50%.
Without the dispersing properties of STP and AEC, the plant was previously spending $5,000 per year in acid to sufficiently depress the pH and was also using deposition and corrosion control chemicals in excess due to the high blowdown rates.
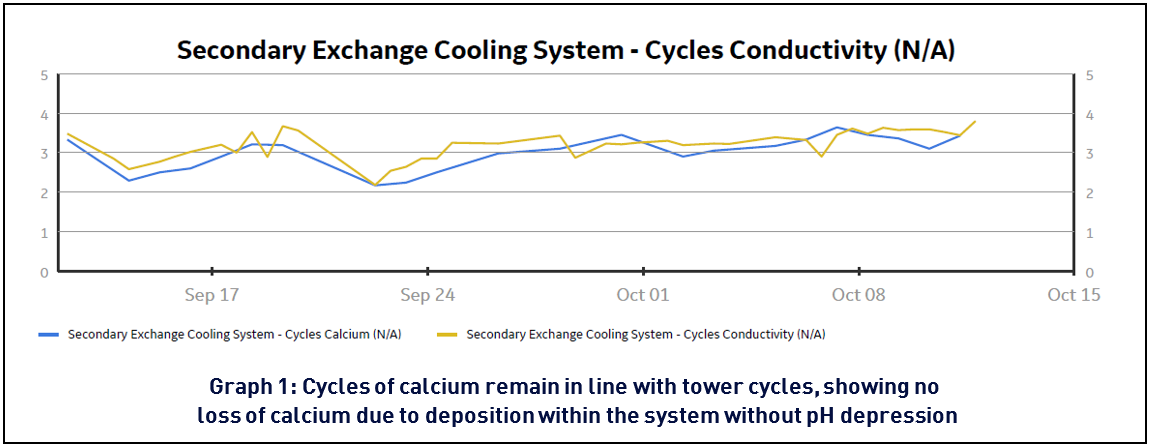
Graph 1 shows that while applying GenGard, cycles of concentration (yellow line) were increased from two to four, with calcium cycles (blue line) showing a similar trend. This indicates that calcium was not depositing, which would be seen with a downward trend. Veolia is now providing a best-in-class water treatment program that is acid-free without causing harmful deposition in the system. The increased cycles reduced the amount of water and chemicals being consumed.
Total savings equate to $28,000 per year and eliminate the environment, health & safety (EHS) risk associated with the use of acid