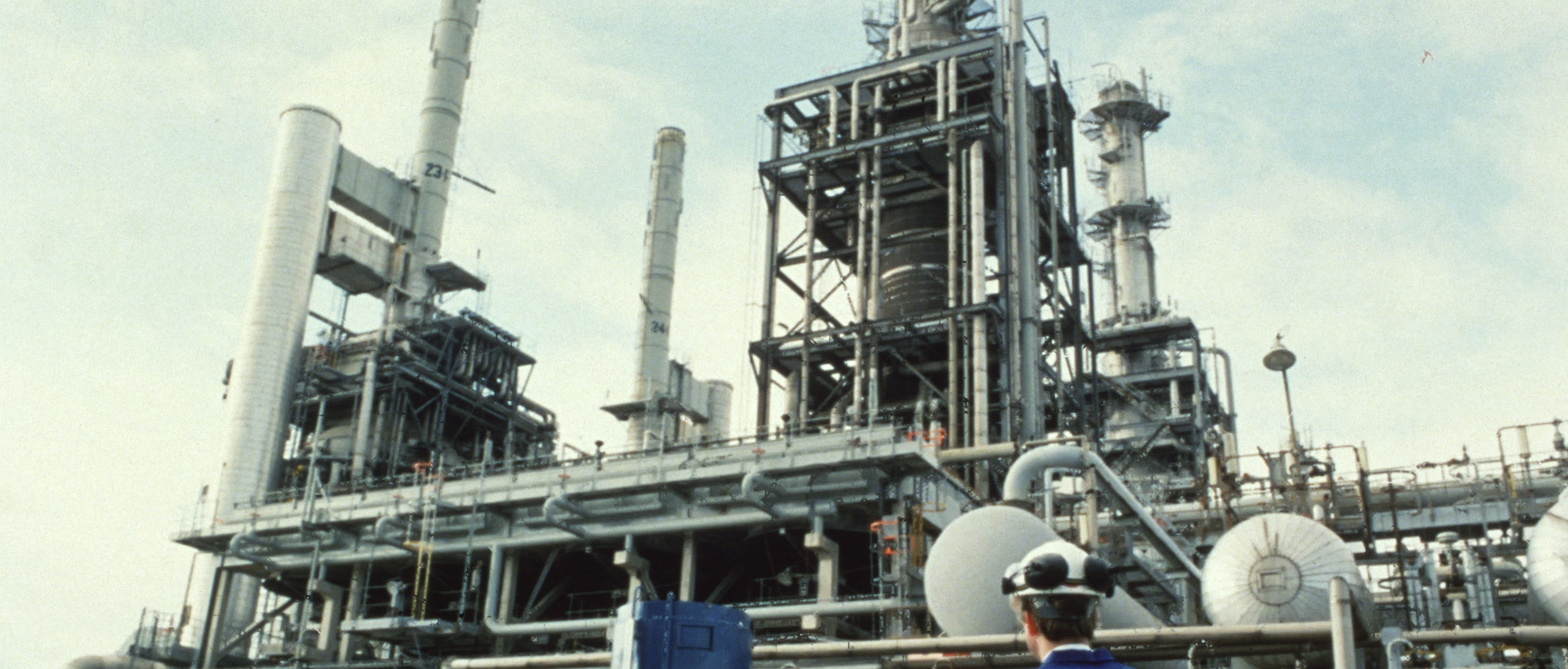
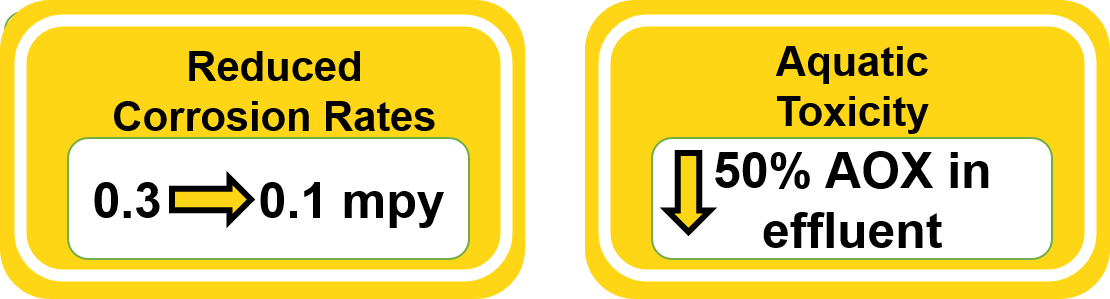
A North American refinery was not consistently achieving their admiralty corrosion rate targets of ≤ 0.3 mpy because of the elevated use of oxidizers, sodium hypochlorite (~1.0 ppm FAC), to maintain acceptable microbiological control in a cooling system utilizing municipal treated reclaim water.
This difficult-to-treat system operates at near-neutral pH (7.0 -7.2) while averaging 1,250 ppm of chlorides in the cycled water. Additionally, the customer was looking to reduce their environmental impact by improving the aquatic toxicity of the products being used and the adsorbable organic halides (AOX). These challenges lead the customer to evaluate a new technology developed using advanced surface science called Engineered Copper Passivation (ECP).
The customer’s cooling tower treatment program was modified from relying on a traditional triazole approach for yellow metal corrosion protection to incorporate our ECP technology. The plan was executed in three phases, with each 30-day phase reducing the azole concentration by 25% of the original value.
Our ECP technology represents a new methodology to passivate yellow metal surfaces compared to traditional azole films. These new inhibitors utilize the various ionic salt species in the cycled cooling water to more efficiently protect the metal surface. Traditional azoles struggle to achieve corrosion targets with elevated free chlorine residuals and often have unfavorable aquatic toxicity and biodegradation profiles.
ECP technology improves both while reducing the inherent and/or transient AOX content that a traditional azole contributes to the cooling tower effluent.
A detailed 180-day field trial was conducted to demonstrate ECP’s ability to improve yellow metal corrosion rates in the presence of oxidizers, reduce the need for azoles by as much as 75% as well as having a positive impact on improving aquatic toxicity and reducing the overall AOX generated in a cooling system.
Result
Admiralty and mild steel coupons were analyzed every 30 days from a coupon rack and an insertion probe on the most critical heat exchanger outlet. The ECP technology demonstrated an impressive reduction in admiralty and mild steel corrosion rates throughout the trial as the azole concentration was being reduced. Figure 1 illustrates the reduction through each phase. Phase 3 demonstrated a slight increase because these coupons were exposed to a FAC residual >100 ppm due to a system upset. These corrosion rates are still lower than the historical values as well as those measured post-trial.
The insertion probe’s admiralty corrosion rates were consistently less than 0.1 mpy throughout the ECP evaluation period. Environmentally, the AOX in the tower discharge was reduced by >50%, and the aquatic toxicity was improved by replacing 75% of the azole with ECP.