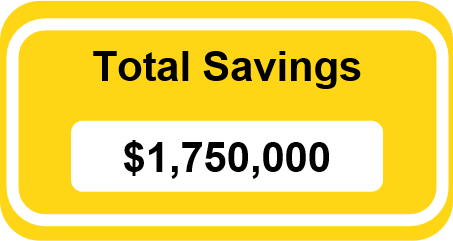
Challenge
An industry leading chemical processing plant producing olefins in North America operates two vertical, shell & tube exchangers (A & B) which use boiler feedwater and steam condensate to remove heat from the process. As these units are prone to fouling from suspended iron particles, regular testing is conducted in the form of Millipore filtration analyses to confirm that iron contamination is maintained to low levels in the units’ influents and effluents.
Historically, both exchangers yielded good iron results, below 50 ppb as Fe, which are measured monthly with Millipores by the Veolia technical representative. After an outage, despite a freshly cleaned exchanger being put online, the iron levels remained high (Figure 1-blue line) so they were swapped after a year of operation and inspected.
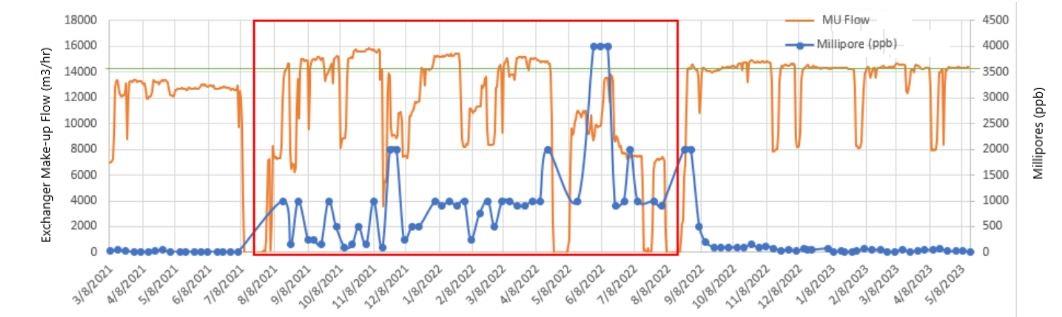
Figure 1: Iron Millipore tests showed high results throughout 2021-2022 (blue line) as steam loads reach 120-125% of design (orange line)
Solution
Tube samples were collected from the middle and bottom sections, and metallurgical analyses were performed at Veolia’s Analytical Laboratory in Tomball, Texas, where elongated gouging and pitting of the metal were observed. Veolia also reviewed the changes in operational practices and audited the water treatment program to ensure best practices were being followed. A full study was completed to understand the internal workings of the vessel.
Design features of the vessel presented unique challenges on the water side:
1) The vessel has no integrated steam drum, using baffles instead. The lack of an integrated steam drum meant there was an internal liquid/vapor interface with a restricted steam disengagement space, making this area prone to corrosion and deposition. The vessel is also more sensitive to water level changes, causing high blowdown rates, especially intermittent blowdowns, which can disrupt internal circulation and cause low water level alarms.
2) While conventional boilers have feedwater entering at the top of the unit, this boiler had feedwater entering at the bottom and just upstream of a bend causing a directional change in water circulation. The cooler boiler feedwater entering in this location may have caused temperature and circulation issues.
3) Due to the presence of baffles, multiple 180° turns in the internal water circulation path makes the exchanger more prone to particulate iron oxide deposition. In addition, if operated above design steam loads, this geometry may be prone to flow accelerated corrosion (FAC) and/or erosion corrosion.
4) Continuous blowdown and boiler water sample points are located near the bottom of the unit. It is best practice to collect continuous blowdown just below the waterline so that the most concentrated and representative water may be sampled. Water collected at the bottom of the unit will show high amounts of settled solids which may not be representative of the general water condition.
The metallurgical analysis of the tube samples showed evidence of elongated gouging and pitting at the bottom of the tubes, but no sign of Flow Accelerated Corrosion (FAC). This could indicate that when the exchanger is operated above 110% of design, conditions exist in the vessel that cause iron loss and/or corrosion, without being related to FAC. This could be due to abnormal boiling condition at high rate, or evaporation to dryness leaving corrosive salts to deposit. In these cases, it was suggested that upgrading shell and tube material to a higher-grade alloy could provide added protection if steam loads are to exceed 110% of design.
Result
After reviewing the operational data, a strong correlation between high iron results and steam loads reaching 120-125% above design was noticed. Previous operation saw peak steam loads reaching 110-115% above design (Figure 1-orange line). The exchanger was put online in June, but unstable plant conditions through the Fall provided unreliable Millipore results during this period. With the plant operation stabilizing after September and with the trial initiated to maintain the steam loads in the exchanger below 120% of design, it was observed that iron levels stabilized and eventually decreased. Millipore is indicative of higher iron level obtained from the sample but does not pinpoint the source of the iron contamination.
To ensure that heat exchangers put online following shutdowns were in optimal start-up conditions, the plant developed procedures for offline cleaning and passivation.
Following operational changes made on the exchangers, where steam loads are now controlled to a maximum of 110% of design, Millipores have returned to normal and continue to be tracked. As a failure of the exchanger would have resulted in a minimum 3-day outage with additional cost of replacement or retubing of the exchanger, the savings were estimated at $1,750,000.
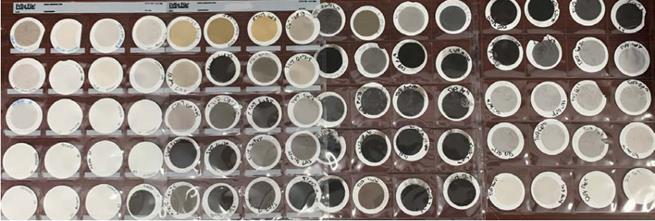
Figure 2: Millipore results showing increasing trend of iron and decreasing iron levels after reducing load below 120%