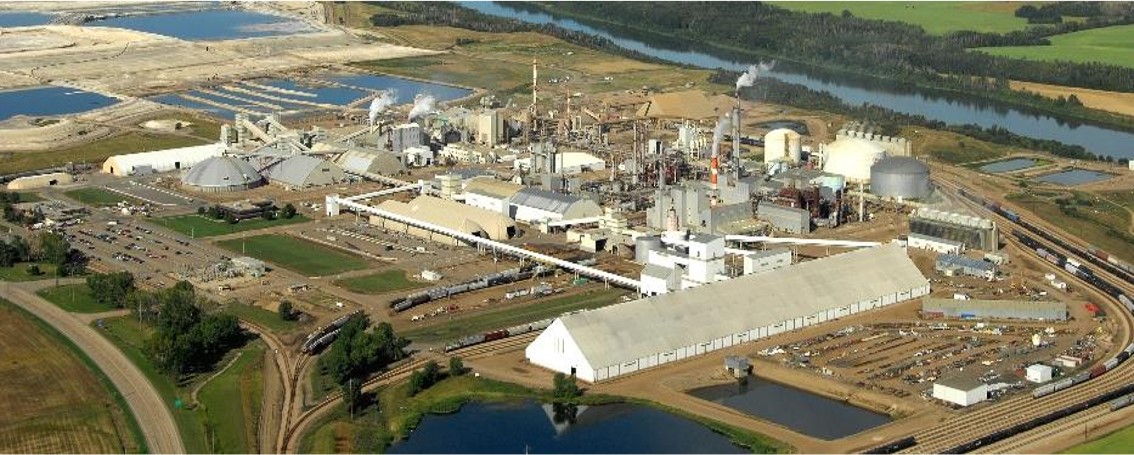
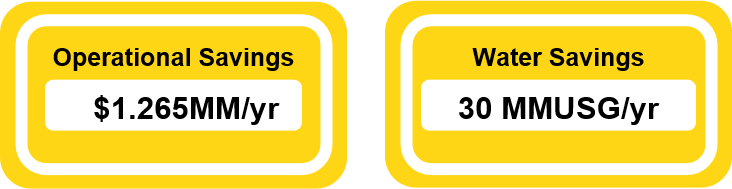
Headquartered in Canada, Nutrien is the world’s third largest ammonia producer with an annual capacity of 7.1 million tonnes. Among its nine nitrogen production facilities is the Redwater Nitrogen Plant. Located in Alberta, Canada, it has a capacity of 1.4 million tonnes per year of nitrogen-based fertilizer.
Nutrien Redwater’s raw water supply comes from the North Saskatchewan River. For much of the year, the river’s water quality is consistently clean. But during the spring runoff, snowmelt introduces large amounts of sediments, increasing turbidity. The plant’s pretreatment system is designed to remove the silt, clay and organic material from the influent water to prevent fouling of the various process equipment, which could lead to performance issues.
Challenge
Redwater’s pretreatment system is comprised of a clarifier and a cold lime softener that normally operate in parallel, sending appropriately treated water to various process areas on site. But during runoff, the clarifier and cold lime softener operate in series, with the clarifier removing the bulk of the suspended solids before being further treated by the cold lime softener. When Veolia partnered with Nutrien Redwater in 2017 to become its water treatment solution provider, the plant had been experiencing operational difficulties coinciding with spring runoff.
Veolia’s local team familiarized themselves with the site’s operation and recognized that the plant’s issues, which included ion exchange demineralizers shortruns, cooling exchanger deposition and plant effluent discharge limit excursions, were not only due to the run-off conditions and pointed to the pretreatment clarification chemistry need for improvement.
Solution
Veolia collaborated with the plant’s operations team, conducting in-depth analytical work during multiple runoff periods to fully capture the impact of the current clarification program. To manage the high influx of suspended solids during these periods, the plant historically fed large quantities of commodity aluminum-sulfate (alum) chemistry. The data collected showed that the high alum dosage during spring runoff was having a negative effect on the cold lime softener outlet water quality, limiting the unit’s ability to remove hardness in the water.
The increased hardness, combined with the increase in dissolved solids for additional sulfate species, was increasing the load on the three ion exchange demineralizers. This was causing the demin trains to be taken offline for regeneration more frequently, leading to an increase in acid and caustic cost, as well as lower water volumes treated due to reduced availability.
Once the Veolia and Nutrien onsite teams had a clear understanding of the root causes of the operational difficulties, they explored how changing the existing clarification chemistry could eliminate the downstream impacts and prevent the demineralizers from acting as a production bottleneck.
Result
After a large-scale trial to test and validate an alternative coagulant chemistry from Veolia’s product suite, the following benefits were confirmed:
- Significantly lower dosage of chemistry added to the primary clarifier
- Improved performance of cold lime softener in hardness removal
- Decreased demineralizers regeneration frequency due to reduced solids loading in influent water (Figure 1)
- Optimized production for increased availability and volume of demineralized water
- Costs savings on acid and caustic usage from reduced regenerations
- Optimized influent water KPI control (Figure 2)
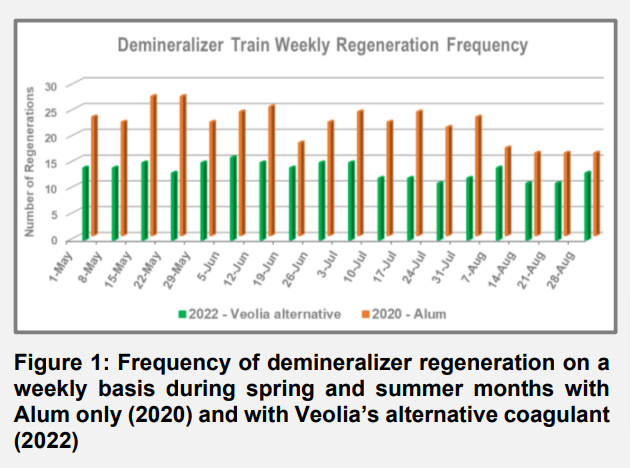
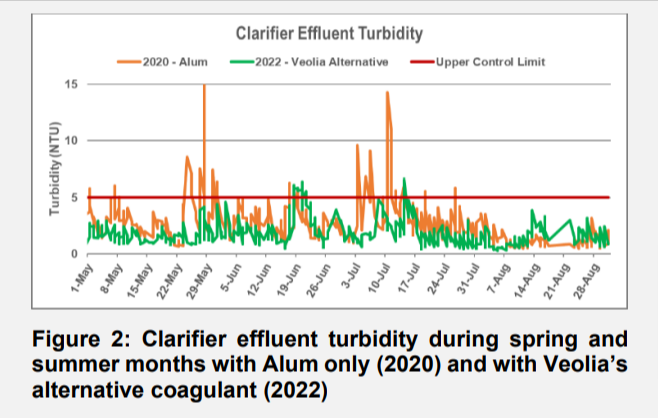
Comparing the plant’s operational parameters under optimized clarifier chemistry against the previous five years, the savings were significant:
- ~30 million gallons per year of water saved from reduced demin regenerations
- $1.265 million in operational savings from improved productivity and reduced chemical usage
“Working with Veolia has not just been great service, but a true partnership. Their expertise in water treatment and application of their programs has increased our performance and improved sustainability with solutions geared toward our specific operation and its challenges.”
Tyler McDowell Chief Power Engineer Nutrien Redwater, Alberta, Canada