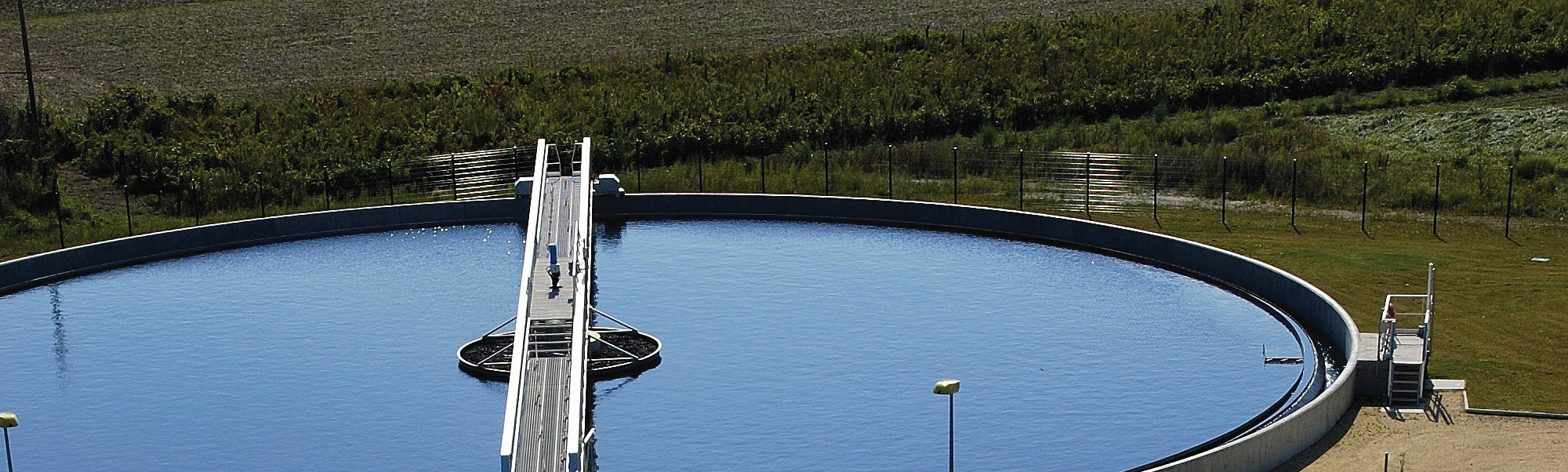

A North American combined cycle natural gas fired power plant clarifies the influent river water prior to filtration, reverse osmosis and ion exchange demineralization polishers. The site has historically used ferric chloride as their sole coagulant for their Densator* clarifier. While the ferric chloride was effective in removing turbidity and enabling filtration to the 0.2 NTU setpoint, it also resulted in a low pH water that was high in dissolved iron and conductivity. This required the use of caustic to raise pH, presenting a risk to operators. In addition, the high soluble iron and conductivity in the clarified water caused fouling and short run-lengths of the reverse osmosis trains, increasing clean-in-place (CIP) frequency and cost of operation.
Veolia engineers collaborated with the plant’s operation’s team on the premise that addition of an aluminum-based inorganic coagulant would enable to satisfy performance metrics while also reducing the handling of hazardous chemicals. Veolia’s on-site team performed extensive jar testing and confirmed that the addition of an aluminum-based KlarAid* coagulant could replace ferric chloride while achieving all KPIs and reducing operating costs.
An on-site evaluation following jar testing provided validation that the bench top simulations transferred to full scale operation. Figure 1 shows both ferric chloride and Veolia’s Klaraid treatment removing turbidity from the influent water during jar test evaluations. The use of aluminum-based KlarAid resulted in less sludge and improved color over incumbent ferric chloride, indicative of lower dissolved solids.
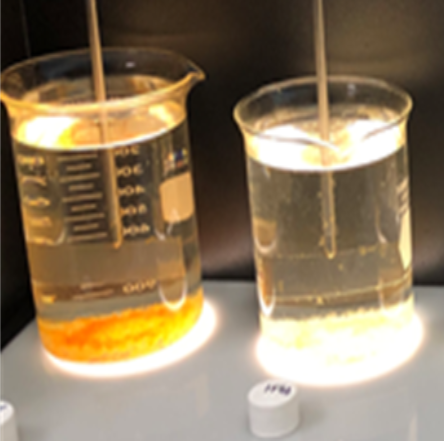
Figure 1: Ferric chloride vs Klaraid jar test
Result
The implementation of the KlarAid coagulant allowed the power plant to continue to meet their filtered water quality specification of less than 0.2 NTU, but with significant operational and economic benefits:
- 80% reduction in soluble iron, reducing reverse osmosis (RO) fouling (Figure 2),
- Lower conductivity of RO feedwater, increasing run-length and reducing CIPs by over 40%,
- Reduction in clarification chemical cost of ~$240,000 per year,
- Increase in gravity filter throughput of 50%, from 300,000 gallons to 450,000 gallons, and reduction of filter backwash frequency by 50%, saving ~4.2MM USG per year,
- ~50% reduction in sludge generation,
- Elimination of caustic and ferric chloride, reducing hazardous chemicals’ handling.
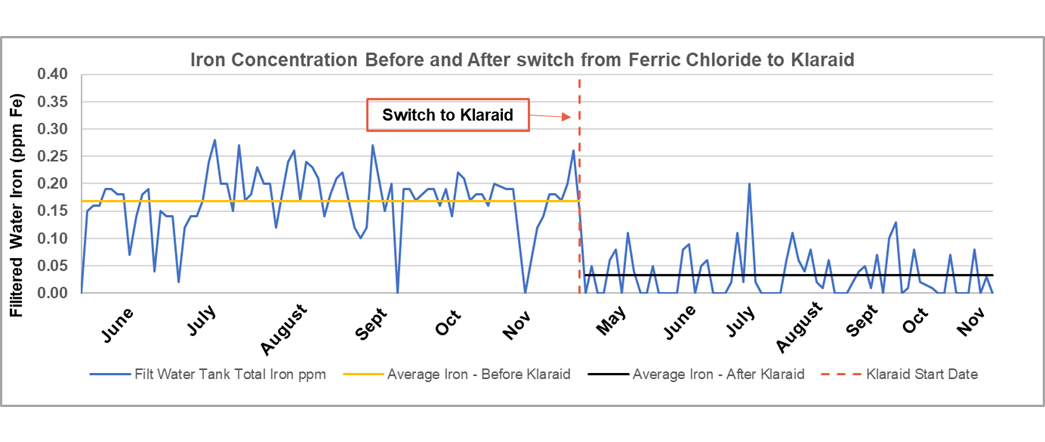