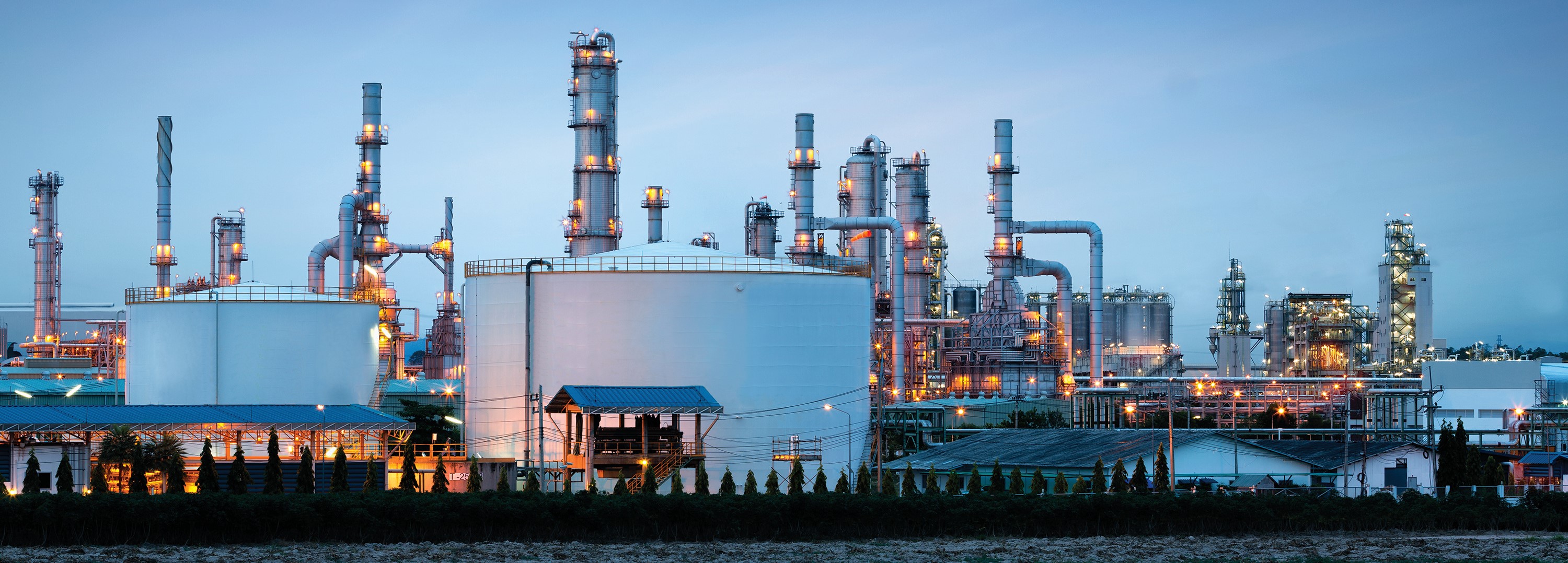
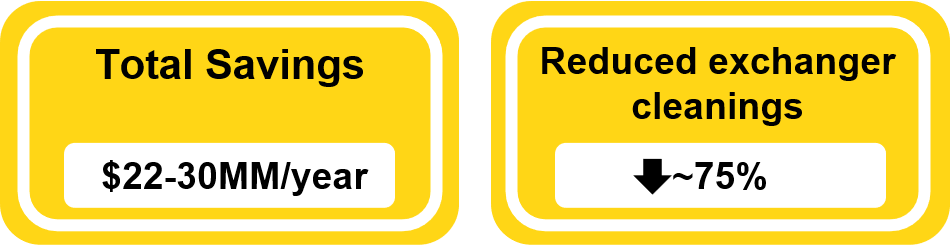
Challenge
In renewable diesel (RD) and sustainable aviation fuel (SAF) production, process heat exchanger fouling is a multifaceted challenge arising from various factors, including accumulation of organic contaminants and inorganic deposits due to the challenging feedstock. Understanding these complex mechanisms is crucial for devising effective mitigation strategies.
This RD producer was having to clean exchangers on average every 60 to 80 days, which represented significant production losses each time the plant had to shut down. Veolia proposed to conduct a thorough investigation of the problem and implement a solution that would reduce fouling and improve process reliability and performance.
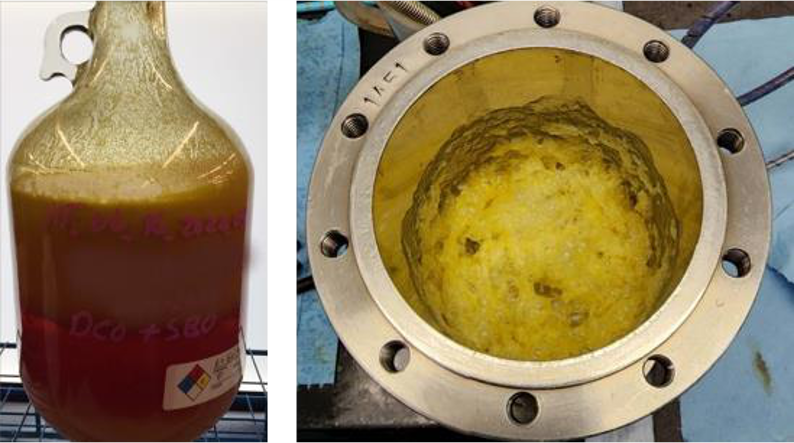
Solution
The composite renewable feedstock processed through the exchanger comprised a blend of various feedstocks, including soy oil and distiller’s corn oil (DCO), along with a recycle stream. The composite feed had a sticky, semi-fluid consistency and complex physical appearance at ambient conditions (Figure 1).
First, Veolia conducted a detailed characterization of the composite feed used in the RDU and its components to identify key parameters that could influence fouling in the heat exchangers (Table 1). Soy oil and DCO exhibited high total acid numbers (TAN), while the composite feed displayed a relatively low TAN (51 mg KOH/g). However, the presence of carbonyls (68 mg/L) and the moderate bromine number (8 g Br/100 g) suggested the potential for fouling due to the deposition of organic compounds and the likelihood of complex reactions such as polymerization and oxidation. The higher bromine number in soy oil compared to that of the DCO, along with DCO’s significantly high carbonyl content (three times that of the composite feed), highlights the individual contributions of each source to the composite feed’s fouling potential. Moreover, soy oil exhibited higher levels of filterable solids and metals, specifically iron, compared to other streams, indicating its potential for inorganic fouling. Although the filterable solids and metals in the composite feed were not exceptionally high, their presence can have a catalytic effect on oxidation and polymerization processes.
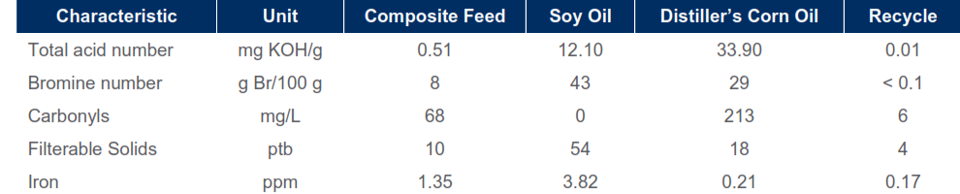
Secondly, Veolia conducted a deposit analysis. The predominant elements found in the deposit included carbon, hydrogen and oxygen, as indicated in Table 3, suggesting the presence of organic compounds and oxygen-containing functional groups. Additionally, sulfur, phosphorus, calcium, potassium, sodium, chlorine and other metals were present in smaller amounts, ranging from 0.1% to 4%. It’s worth noting that sulfur can exist in organic as well as inorganic forms in renewable fuel production processes. The presence of these elements suggests a combination of organic contaminants and inorganic deposits contributing to fouling in the heat exchanger.
A treatment testing procedure was designed to assess the effectiveness of different dispersant and polymerization inhibitor chemistries, denoted as Products A, B and C, using a thermal fouling testing rig. This testing apparatus mimics the conditions of a heat exchanger by passing the sample through a shell-and-tube heat exchanger, where a heating rod serves as the heating element. Fouling deposition occurs on the heating rod, reducing heat transfer measured by a gradual decline in outlet fluid temperature (∆T). Antifoulant efficacy is determined by averaging outlet temperature drops over a specified time period and expressing the percentage reduction in fouling relative to untreated conditions.
Figure 2 reveals progressive fouling accumulation and reduced heat transfer efficiency of the different treated and untreated samples. Product A consistently exhibited the lowest increase in ∆T among the treated samples, with an averaged 75% fouling reduction.
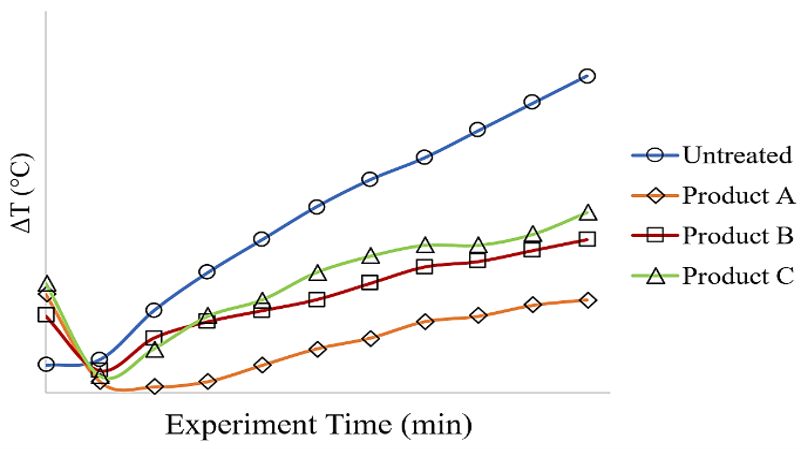
Result
Veolia commercialized Product A as part of its Thermoflo* BIO product line in order for it to be trialed online at the refinery. Thermoflo BIO are specialized products for biofuels processing. Notable improvements were observed in heat exchanger performance in the following weeks and months. The RDU operated for over 340 days without any shutdown associated with exchanger fouling, where prior operation required outages for cleanings every 30 to 80 days. Although there was a shutdown during the trial period, as shown in Figure 3, it was due to an unrelated maintenance activity.
By preventing quarterly shutdowns over a 12-month period, productivity improvement translated into $22- 30 million of additional revenue. Furthermore, the elimination of each exchanger cleaning saved the producer an estimated $40,000 in maintenance costs.
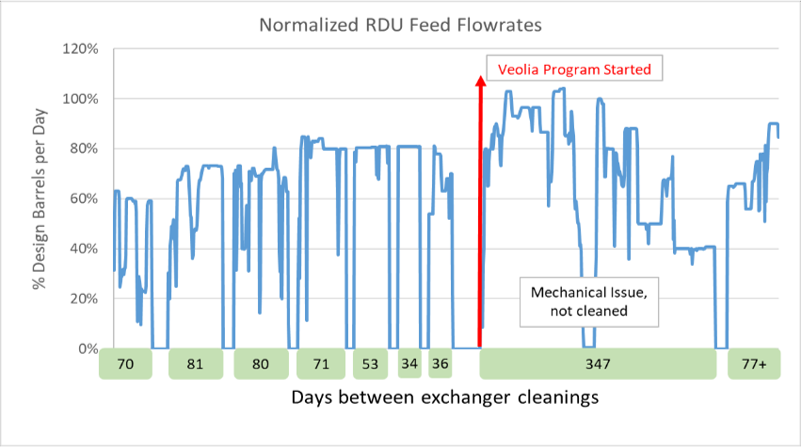