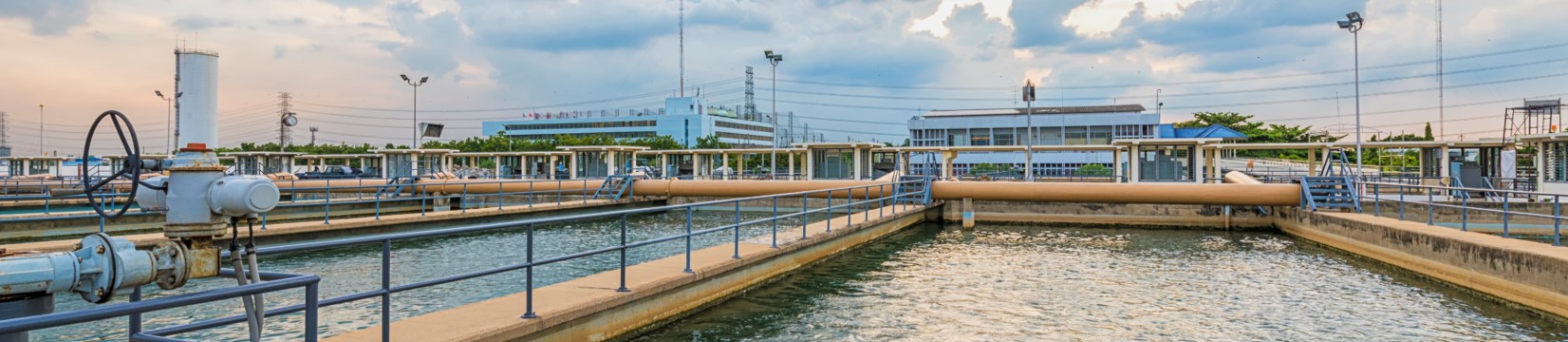
To meet corporate sustainability goals, a leading ammonia fertilizer manufacturer in the United States faced the environmental challenge of reducing landfill volume from disposed waste. The facility used disposable 1-micron cartridge filters to remove wax from their UAN prill dissolving pit.
The extremely rapid fouling rate of the filtration elements created a need for frequent change-outs. This operation required, on average, 400 cartridges each day, totaling almost 150,000 units annually. Excessive consumption of filters represented a significant replacement, high disposal cost, and increased volume of waste sent to landfills.
Veolia engineers audited the system and recommended using a dissolved air flotation (DAF) unit with KlarAid* coagulant and PolyFloc* flocculant treatment to remove the wax from the UAN process stream.
Jar tests were conducted to develop the treatment program, followed by an on-site evaluation using pilot-scale flotation equipment. Figure 1 shows the result of the Veolia chemical treatment in separating the waxy contaminants during jar test evaluations in the laboratory.
Figure 1: Jar test results of UAN stream wax removal treatment
Result
The combination of DAF and Veolia treatment products followed by filtration polishing allowed the ammonia manufacturer to continue to meet their treated water quality specification of <10 NTU of turbidity, but with significant operational, economic, and environmental benefits.
With the implementation of the DAF and chemical treatment followed by filtration polishing, the number of filter elements used each year was reduced from 146,000 to 12,000 units, or approximately 30 per day. This led to a reduction of 92% in associated costs and a reduction in the landfilled waste volume of 590 cubic yards per year.
Use of the DAF and chemical treatment compared to previous filter-only operations led to:
- A reduction in filter cost of ~$450,000 per year;
- Reduced volume of used filters landfilled by 590 cubic yards, resulting in an annual savings of approximately $50,000; and
- A more consistent reclaimed product as filter fouling and change-outs caused variations in quality compared to the stable DAF operation.
For the first year of operation, the new DAF equipment and treatment represented a cost for the plant of approximately $182,000. The return on investment (ROI) for this project, based on a prior spend of approximately $500,000 annually for the filter-only application, saved the plant almost $318,000 in operational costs.