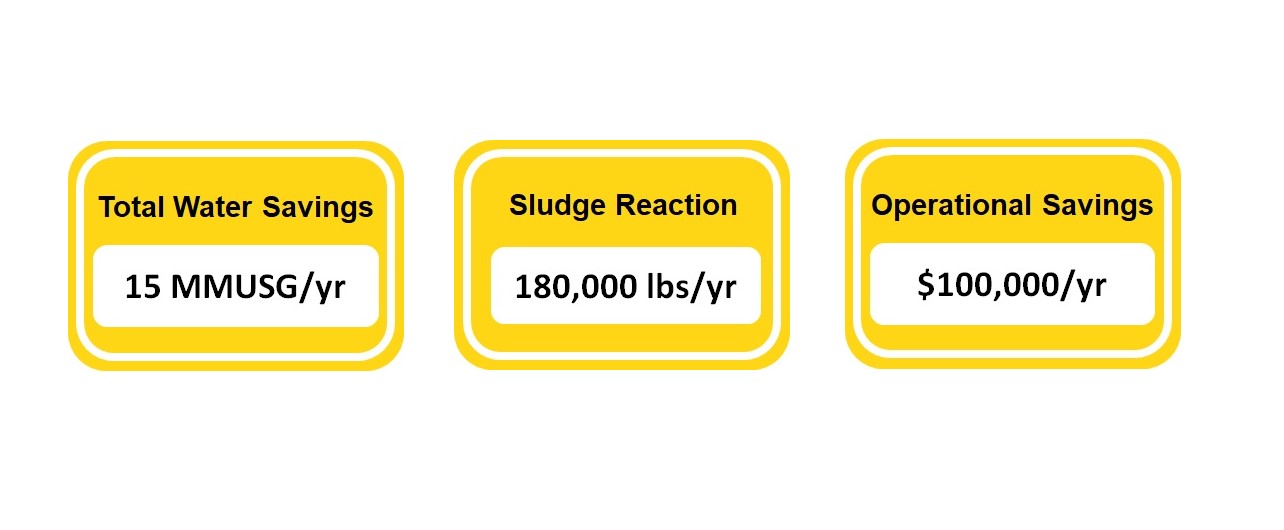
Challenge
One of the largest US semiconductors producer manufactures integrated circuits in a fab in the Southwest. There, they also conduct research into new ways of fabricating semiconductors, including methods to reduce chemical and water use.
Large amounts of ultrapure water were required for their state-of-theart manufacturing process. Because the wastewater from the laboratory sometimes contained residual chemicals, the entire volume of spent water was continuously treated to meet discharge standards. The treatment was expensive, required large amounts of chemicals, produced significant quantities of sludge, and ultimately wasted a lot of water – a scarce resource, especially in the Southwest US.
Solution
In a joint project with Veolia, this microelectronics facility made plant improvements to divert, store and test the wastewater so that treatment chemicals were only added when necessary. The treatment program focused not just on compliance but on finding even better ways to prevent pollution, minimize chemical consumption and reuse valuable water.
Result
The new water management program cut this facility’s annual use of chemicals by about 350,000 lbs, eliminated more than 180,000 lbs of sludge, and made it possible to reuse nearly 15 million gallons per year of essentially “clean” wastewater in the plant’s cooling towers. Because the reused water was so clean, it allowed the cooling towers to cycle up to nine cycles.
In addition to its environmental benefits, the new water management system is saving this microelectronics facility more than US$100,000 a year in net costs for water, chemicals and sludge disposal. The improvements have also reduced the impact of operations on the municipal sewage treatment system.
Click here to learn more about our solutions for the Semiconductor Industry