
Challenge
Federated Co-operatives Limited’s Co-op Refinery Complex (CRC) is one of the single largest freshwater consumers in the city of Regina, Saskatchewan. Embracing conservation, the oil refinery committed to a $200 million environmental mega project – referred to as their Wastewater Improvement Project – focusing on sustainability and environmental stewardship.
The project is the culmination of the facility’s production expansion from 100,000 barrels per day (bpd) to 130,000 bpd, all while using less fresh water and discharging less wastewater. The expanded operation needed an advanced wastewater treatment facility capable of:
- Removing solids, oils, phenols, nitrogen compounds, organics, and other contaminants.
- Eliminating the release of volatile organic compounds from wastewater ponds to the atmosphere.
- Demineralizing treated water for use in steam production.
- Eliminating the use of municipal treated water and reducing demand on groundwater.
Solution
Veolia Water Technologies was called in to help design, build, and commission portions of CRC’s unique wastewater treatment solution. The five-stage system, illustrated in Figure 1, employs many of Veolia’s advanced water treatment technologies.
During stage 1, wastewater is delivered to holding tanks where gravity separates oil and water. Oil is skimmed off the top as it floats above the water and is reprocessed within the refinery. The wastewater is taken to another tank where sediment and oily sludge sink to the bottom. The oil is sent back to the refinery for reprocessing and the sludge is removed and disposed of safely.
The remaining wastewater continues to stage 2, a Veolia Poseidon* dissolved gas flotation unit. Microscopic bubbles of nitrogen are pumped into the unit to bind to suspended oil particles. These particles are brought to the top of the unit, where they are removed for reprocessing. Stage 2 utilizes Veolia’s PolyFloc* AE1701 chemistry as a flocculant.
After separation, the wastewater enters stage 3, biological treatment followed by filtration through Veolia’s ZeeWeed* 500 ultrafiltration hollow-fiber membranes. This combination, known as membrane bioreactor (MBR) technology, creates permeate (see Figure 2). Stage 3 utilizes Veolia’s BioPlus* BA2970 & BioPlus* BA3900 chemistry for biological seeding and bioaugmentation on the biological reactor. FoamTrol* AF3031 is also utilized in the biological reactor for foam control.
Largely free of organics, ammonia, nitrites, nitrate, and other impurities, the permeate moves directly to the demineralization plant (stage 5) for further treatment to prepare for steam production.
The main function of stage 4 is to handle the excess biomass from the bioreactor. This biomass is sent to a centrifuge to separate and return bacteria to the bioreactor. A small amount of water is extracted and reprocessed, while the leftover solid biomass is disposed of safely. During this stage, Veolia’s Novus* CE2655 chemistry is used as a flocculant in the centrifuge.
Stage 5 is the demineralization plant, which will finalize the recycled water for steam production by treating high levels of dissolved solids. The plant will feature Veolia’s High pH RO system, which consists of ion exchange units for hardness reduction and a decarbonator to remove alkalinity and carbon dioxide. High pH RO is unique in its ability to effectively run at a very high recovery, under high organic loading, without fouling or frequent cleaning.
Following the removal of dissolved solids like calcium, magnesium, chlorides, and sulfates, the permeate takes a second pass through another RO to polish the water and finishes with mixed bed demineralization to produce ultrapure water (see Figure 3).
In addition to equipment and chemicals, Veolia provides InSight* asset performance management for stages 2, 3, and 4 of the CRC process. InSight uses data and analytics to ensure water treatment assets operate at optimal performance. During stage 3, Veolia’s equipment team uses InSight to monitor the performance and long-term health of the ZeeWeed membranes. The Veolia team uses InSight to focus on the operation, chemistry, and overall product quality between stages. For example, they monitor the removal of solids, oils, and greases across stage 2 and look closely at water quality leaving stage 3 to ensure it’s on spec to reuse during stage 5. Lastly, Veolia uses InSight to monitor chemical use and dosage ranges, as well as tank inventories. This ensures chemicals are dosed correctly, ordered when needed, and always available.
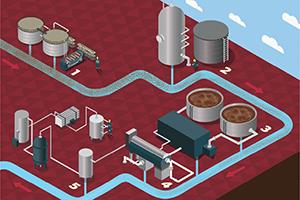
Figure 1: The CRC Wastewater Improvement Project features a fivestage wastewater treatment solution that enables the recycling and reuse of 2 million gallons of wastewater a day.

Figure 2: During Stage 3, Veolia’s ZeeWeed ultrafiltration membranes filter the wastewater for reuse.
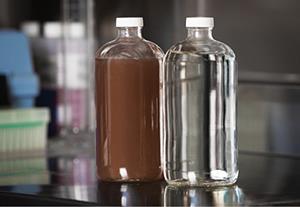
Figure 3: Untreated wastewater from CRC (left) and Veolia-treated wastewater (right)
Result
The combination of ZeeWeed MBR and High pH RO will allow CRC to eliminate all wastewater effluent, most of which is recovered for use in the refinery’s steam plant; without this solution, the facility would produce 2 million gallons of wastewater a day. This comprehensive solution will decrease the complex’s reliance on raw water from the City of Regina aquifier and will reduce the refinery’s freshwater needs by 28 percent. This is the equivalent usage of about 3,100 Regina households on an annual basis.
Furthermore, a unique combination of live bacteria, special filtration units, and Veolia’s state-of-the-art High pH RO technology will significantly reduce the complex’s environmental footprint. This is achieved with the reduction of emissions and nuisance odors from volatile organics in the complex’s water-holding ponds.
In 2017, the CRC’s Wastewater Improvement Project was named Industrial Water Project of the Year by Global Water Intelligence (GWI). The award recognized the Veolia project as the year’s most impressive technical or environmental achievement in the field of industrial water.
While a sizable investment, the multi-million-dollar project serves as a foremost example of how a business can operate—and even expand—while being mindful of the environment and water scarcity issues.