Tacora Resources Inc. owns and operates iron ore mining operations, including the Scully Iron Mine in the town of Wabush, NL, located in Atlantic Canada. The company aims at developing and operating iron ore extraction sites in a sustainable and progressive manner, providing a critical resource while remaining conscientious of the community and the environment.
Tacora normally operates electrical boilers to generate the steam required by the site’s iron ore concentration process. These “electrode” boilers do not use fuel oil, unlike conventional combustion boilers, so their carbon footprint is significantly lower.
Due to the failure of one of their electric boilers (#1), Tacora needed to start-up its idled combustion boilers to maintain production rates. Tacora approached Veolia to inquire about its water treatment capabilities and how it could help the mine maintain production while preventing the environmental impact of fuel oil combustion.
Veolia has a wide portfolio of water and process treatment capabilities, including equipment, chemistry and services. It was already a supplier of specialty chemicals at the mine for its steam boilers and wastewater treatment, and was well versed in the Scully mine’s steam plant operation.
The electric boiler #1 that had failed was fed softened water, using ion exchange resin softeners. The remaining electric boiler #2 was designed to only use high purity condensate returns from the steam generated by boiler #1 that was now out of commission. Without condensate return available, steam could only be generated by using softened water into the back-up oil-fired boilers.
Tacora knew that Veolia was also a manufacturer of reverse osmosis (RO) membranes and other water purification systems, which could help treat boiler feedwater to meet the quality required by electric boiler #2.
The steam plant’s superintendent asked the Veolia technical representative if we could rapidly provide a treatment solution that would sustain steam production through electric boiler #2.
The Veolia representative rapidly conducted a full audit of the steam plant’s operating conditions to evaluate the appropriate solution to implement. Considering the water quality requirements of electric boiler #2 and properties of the available feedwater, it was recommended that an ion exchange demineralizer be used instead of an RO system. The ion exchange “demin” would better sustain operation with the high level of suspended solids present in the feedwater.
Veolia has the largest fleet of mobile water purification systems in North America, which can be made available as an emergency dispatch service. A set of mobile demineralizer trailers was rapidly outfitted with the proper equipment to satisfy the needs of Tacora’s electric boiler #2.
In as little as 2 weeks from the initial boiler failure, the mobile demineralizer trailer traveled to the mine and was hooked to the steam plant’s boiler feed water system (Figure 1). When the trailer arrived, Veolia personnel put it in service and, for over 2 months, it supplied high purity water to the electric boiler. This allowed for time where parts were delivered, and repairs were completed on its counterpart.
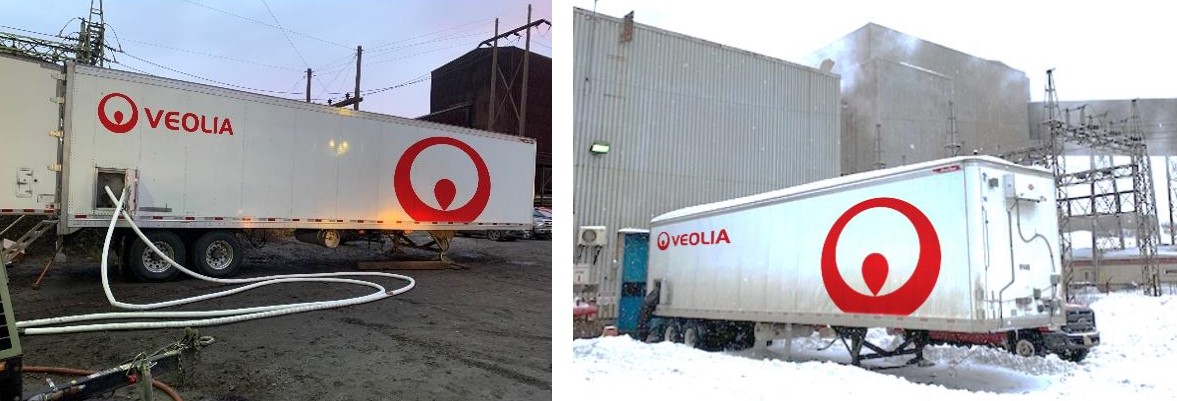
Figure 1: Veolia's mobile demineralizer trailer at Tacora Resources Scully Mine
Result
The high purity water produced by the mobile demineralizer system allowed electric boiler #2 to operate at full capacity for the whole duration of the project, without impact to the mine’s production.
Veolia’s representatives provided support to the steam plant operators for the duration of the project to ensure optimal operation of the system.
If the oil-fired boilers had been used for that 2-month period instead of the electric boiler, they would have used over 25,000 L of bunker oil per day, which would have emitted over 5500 tons of CO2.
The costs associated with fuel, water and chemical treatment that were saved through the implementation of this mobile water treatment project were evaluated by the mine at $1.35MM.
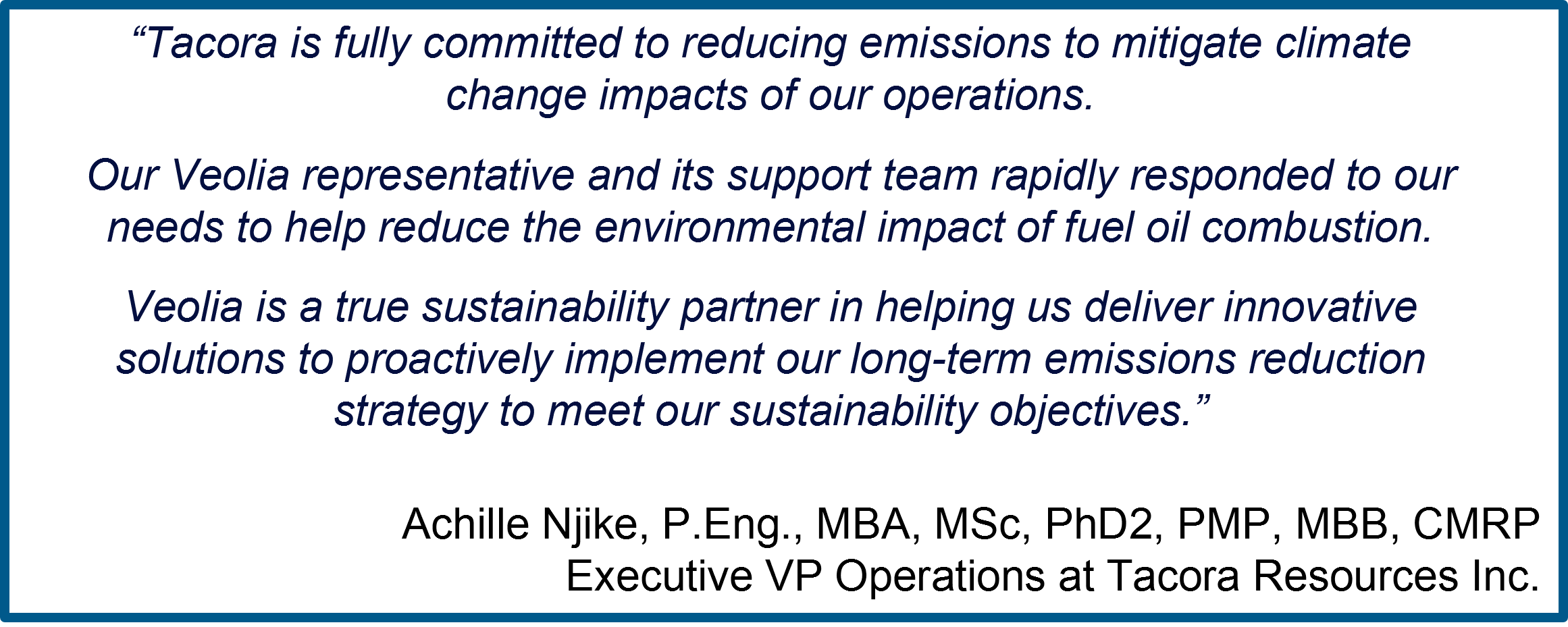