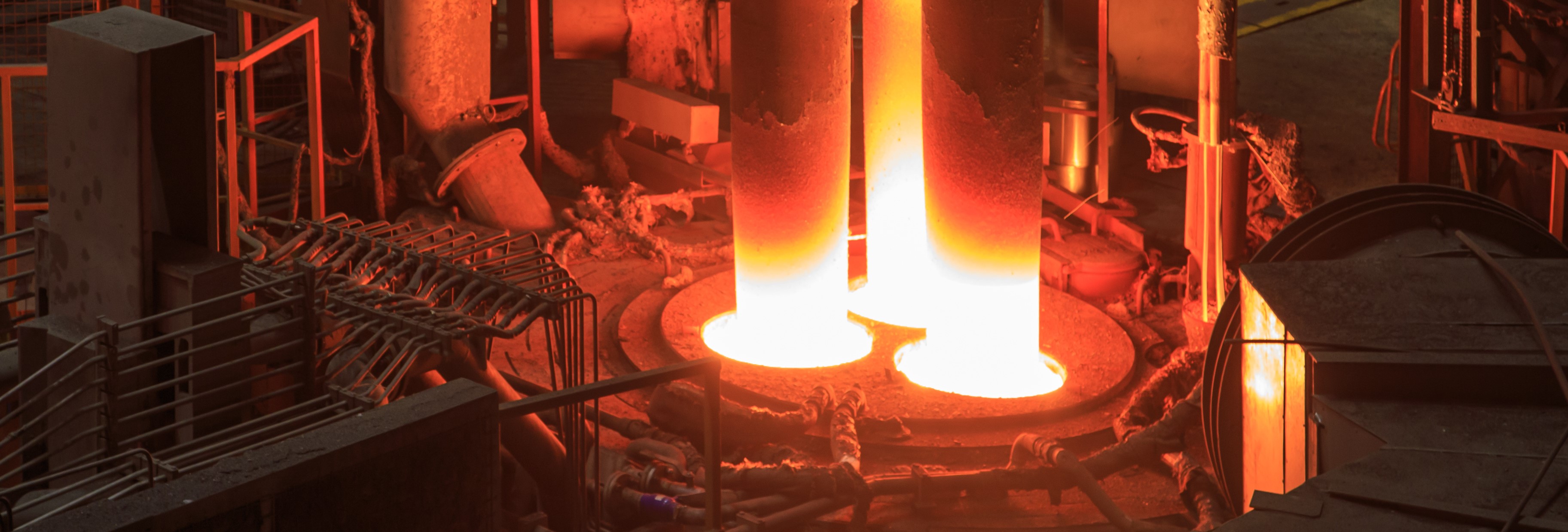
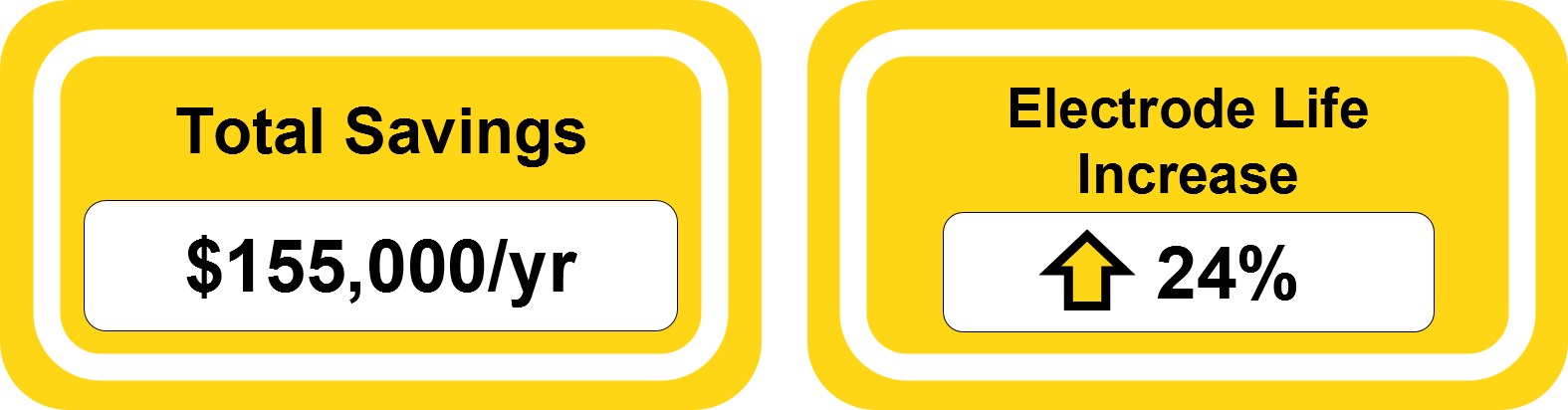
Graphite carbon-based electrodes are used for melting steel in the electric arc furnace of most mini mill meltshops. The electrodes are a critical part of the steelmaking process as they transfer high amounts of electric current and convert it into the heat that is used to melt scrap metal. Electrodes are consumed during the melting process as they produce an arc to generate heat. Improper electrode cooling causes excessive wear and shortens the life of the electrodes.
A North American steel mill was experiencing high usage rate of the Phase 1 electrodes, increasing cost of operation. As the issue was related to only one of the electrodes, the mill inquired with Veolia about improving the electrode cooling flow monitoring. It was suggested that the data be tracked in Veolia’s InSight* cloud-based data management system which was already in use for other applications at the mill. The customer felt that a better understanding of the cooling water distribution could help mitigate the issue and reduce production costs.
Before proposing any kind of chemical treatment, Veolia conducted a study with the steel mill’s engineers to evaluate cooling water flow control to each electrode. Each electrode contains spray rings with very small openings that distribute cooling water onto the electrode’s surface to provide proper cooling water coverage and optimum heat transfer efficiency. The spray pattern requires a specific amount of water designed to minimize sidewall oxidation and electrode wear.
The flows to each phase of the electrodes were uploaded into InSight and the flow patterns were monitored over several heats. This helped determine that the setpoint for Phase 1 electrode was not being met, as it was 0.5-1.0 gpm below the target, or 15% too low (Figure 1).
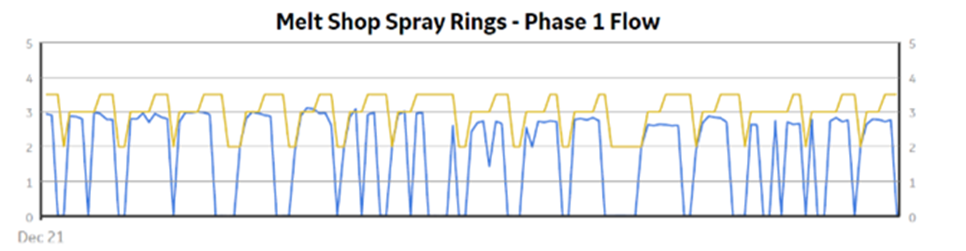
Figure 1: Phase 1 flow (blue) not reaching setpoint (yellow)
To confirm that the Phase 1 flow was in fact below its setpoint, the flow signals from Phases 1 and 2 were swapped. The data analyzed from Veolia’s InSight cloud-based data management system showed a flow restriction on the cooling water line as the reason for the lack of water. This led the customer to do some additional investigation of the piping and found one of the lines had crimped, pinching off flow to Phase 1. This situation was fixed, and flow rates were restored.
Result
Once flow to Phase 1 cooling line was restored, the cooling flow reached the setpoint (Figure 2). These appropriate flow conditions significantly increased electrode life, by an estimated 24%.
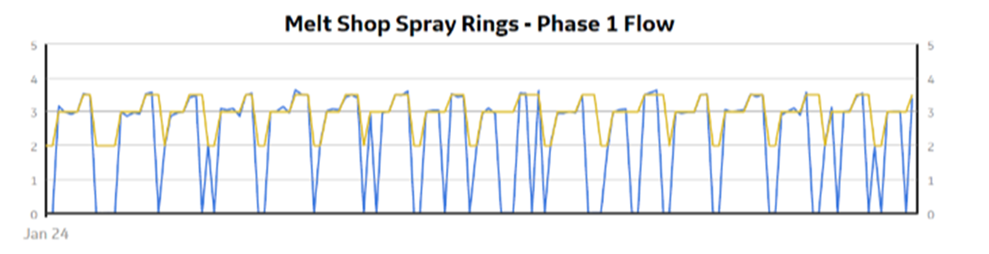
Figure 2: Phase 1 flow (blue) reaching setpoint (yellow) upon finding line restriction
using flow and InSight cloud-based data management analysis
The data obtained during this test period indicates a step change in the number of heats sustained by the Phase 1 electrodes: from 13 heats up to 17 heats per electrode. This reduction in electrode corrosion from optimized cooling flow saved the steel mill approximately $155,000 per year.
Beyond the concern of electrode consumption, avoiding uneven sidewall oxidation is critical to ensure proper arc transmission to the steel bath. Hence, ensuring proper cooling water flow through systematic monitoring can help maintain productivity, quality and reliability of the process without necessarily requiring additional chemical treatments.