Internal Treatment Chemicals
Increase boiler efficiency and reliability through deposition and corrosion control with Veolia’s boiler internal treatment chemistry
Increase boiler efficiency and reliability through deposition and corrosion control with Veolia’s boiler internal treatment chemistry
Deposition and corrosion of boiler systems reduce efficiency, increase fuel and water consumption, and may lead to failures, which are a safety hazard, add maintenance costs and may impede production. Veolia’s boiler water internal treatment programs provide highly effective protection against corrosion and scale formation to ensure optimum performance and availability of your steam system while reducing the total cost of ownership and environmental footprint through energy and water savings.
Product Highlight
Features & Benefits
Case Studies
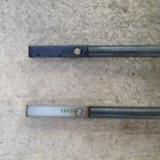
Volatile Polyamine technology saves acid plant an estimated $135,000 annually
An acid plant in the Southern US was experiencing high mild steel condensate corrosion rates.
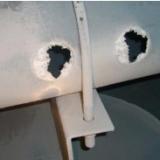
HTP Polymer mitigates effects of contaminated feedwater for power producer
An independent power producer in Ontario experienced trace amounts of impurities in its feedwater.
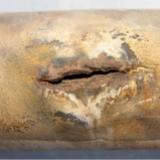
Boiler on-line cleaning returns $3.2M per year of savings by avoiding unscheduled shutdowns
A chemical company in Turkey experienced boiler tube failures on the water side due to overheating caused iron oxides to build up.
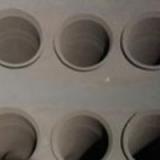
Solus AP helps pulp & paper client improve boiler efficiency
A pulp and paper customer experienced recurring feedwater hardness ingress which reduced boiler efficiency by limiting heat exchange.
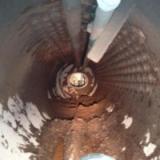
New all-polymer internal boiler treatment demonstrates flexibility and forgiveness in variable conditions
A US college’s main condensate return lined from campus was out-of-service for excavation and repairs.
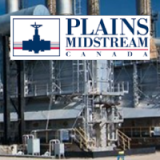
Gas plant reduces environmental footprint & improves performance with Solus* boiler polymer
Veolia provided a solution that reduced phosphate discharge, water and chemical consumption, as well as carbon emissions to Plains Midstream, a gas plant in Southern Alberta.