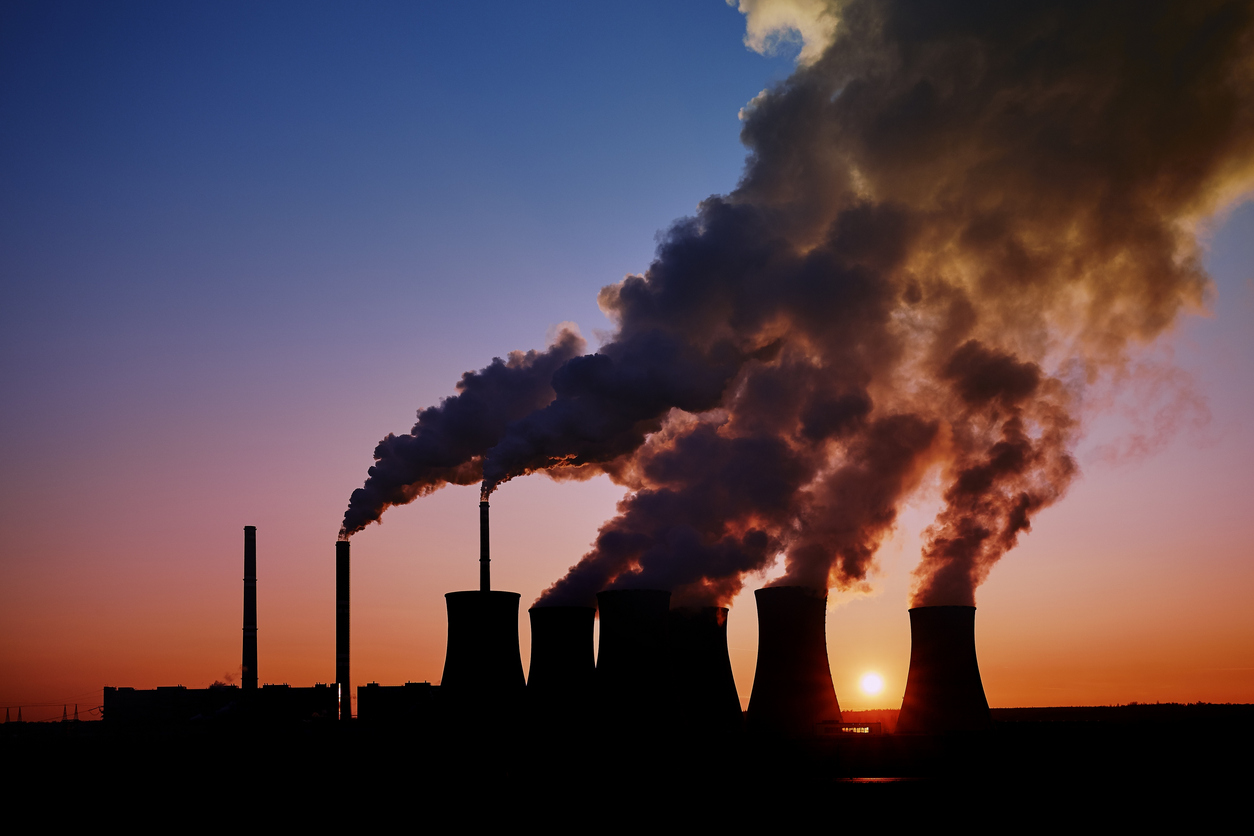
Utilities for heating and cooling are critical to production processes across industries. Often these utilities use water for steam generation or to remove heat. Ultrapure water is a critical component in steam generation systems across many industries, including food and beverage, refineries, chemical processing, and power. For steam generation, water goes through extensive treatment processes to remove contaminants before being used and then is often recycled or discharged after use. Proper water treatment plays a key role in maintaining productivity, asset protection, and enabling water reuse.
Total organic carbon (TOC) can be a latent corrosion contributor which can enter water systems from the original source water or get introduced through cooling processes, leaks or other contamination points. If not removed, these organics can break down into corrosive acids at the high temperatures and pressures inside boilers and turbines. This corrosion can lead to equipment damage, deposits, unplanned downtime and reduced efficiency.
Some common sources of organic contaminants include:
- Source organics that pass pre-treatment Ion-exchange resin or resin itself leaching
- Treatment chemicals that volatilize into steam
- Lubricating oils or degreasing solvents Leaks from process side
- Polluted condensate returned to the boiler
- Residue organics that cause microbial growth
To protect assets, some boiler insurance providers and regulatory bodies enforce strict TOC limits as low as 100-200 parts per billion (ppb) and some plants operate as low as 10% of that. Organics like polysaccharides can also foul membranes used for water purification. Monitoring and removing organics saves costs through improved equipment reliability and efficiency.
TOC monitoring allows plants to detect organic contamination from source water, identify treatment deficiencies, find leaks, and troubleshoot other issues. For example, measuring changes in organic content can identify breaches in system processes, and monitoring control points can help troubleshoot and identify sources of pollution. The information and data obtained from TOC monitoring allows for fast decision making to protect valuable equipment and achieve operational goals.
As plants move towards zero liquid discharge and increased water reuse, TOC data helps determine which streams can be safely recycled. TOC data provides facilities with information to solve various problems that can occur when monitoring ultrapure water.
Problem | Solution |
---|---|
Corrosion cracking in last rows of the steam turbine when source water changed from drinking water to industrial water. | Monitoring TOC when changing source waters or monitoring for changes in source waters can indicate if treatment adjustments are needed. |
Defective anion exchange resin passed chlorinated organics into steam cycle. Increased chloride concentration forced a boiler blow-down. | Even though the resin rinsed to acceptable conductivity levels, non-ionic chlorinated organics did not rinse out. TOC monitors ionic and non-ionic organics and can help troubleshoot issues with process equipment. |
Boilers needed replacement every two years due to internal scaling. Foaming was noticed on saturated steam lines. Investigation revealed TOC had reached 200 ppm in condensate return lines. | Continual monitoring of makeup and condensate for TOC can prevent scale from building up and protect equipment from damage. |
Organics monitoring provides an effective way to measure and control organic contaminants while minimizing corrosion, fouling and other issues that impact productivity, costs and asset lifetimes. With increasingly stringent regulations and water reuse targets, TOC monitoring is an essential tool for optimizing water treatment in various steam generation processes.
To learn more about how implementing organics monitoring into your steam generation processes can be beneficial to you, click here.