Dry Milling Ethanol Treatment Solutions
In the dry milling corn-to-ethanol process, operators are continually seeking ways to improve process efficiency and lower operating costs to help drive the overall profitability of the plant and increase competitiveness.
Veolia offers a comprehensive portfolio of treatments, equipment and analytics solutions to help ethanol producers increase yield, manage downtime and reduce total cost of operation.
Process Overview
Key applications
Boiler Water Treatment
Prolong the life of your physical assets and maximize process productivity by optimizing…Cooling Tower Water Treatment
Corrosion, deposition, fouling, and biological growth can derail your operations. Veolia…Industrial & Municipal Wastewater Treatment
Whether municipal or industrial, Veolia understands your challenges and recognizes the…Monitoring Systems
By monitoring your industrial water and wastewater processes, you can protect assets,…Key products & services
Boiler Water Chemicals
Driving efficiency, safety and reliability in your steam-generating systemCooling Water Treatment Chemicals
Extend asset life with Veolia's broad portfolio of cooling water treatmentsWater & Wastewater Service Programs
Improve your operations with Veolia expertise and service offeringsMembrane Chemicals & Pretreatment Products
Protect your RO membranes from scale, bacterial growth and foulingFoodPro* Soft Water Corrosion Inhibitors
Fight soft water corrosion with molybdate-free chemistryInSight*: Asset Performance Management
Get connected. Get InSight. Get optimized.Case Histories
Water reuse helps White Energy save over $200,000 per year
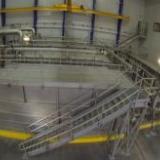
Veolia technology enables the world’s first zero liquid discharge (ZLD) corn mill
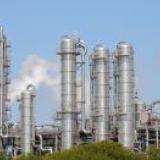
Ethanol facility increases run-length and production capacity with Veolia FoodPro*
A large ethanol producer in the mid-west recognized that the ethanol evaporation process from fermented beer mash had a significant fouling potential that could severely impact plant operations.
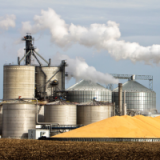
Ethanol plant’s cooling towers treated with E.C.O.Film* improves corrosion protection and meets stricter phosphorus regulation
The increased concentration of phosphorus in bodies of water leads to unnatural algae growth, upsetting indigenous f
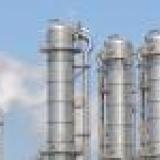
Ethanol plant reduces evap CIP cleanings frequency and improves efficiency with IVAP analytics
Ethanol plant reduces evap CIP cleanings frequency and improves efficiency with IVAP analytics